Transforming Industries – One Solution at a Time
Dive into the success stories of diverse industries, where Ramp’s customised RFID solutions and deep industry knowledge have redefined efficiency and productivity. Experience the power of partnering with Ramp.
Filter by
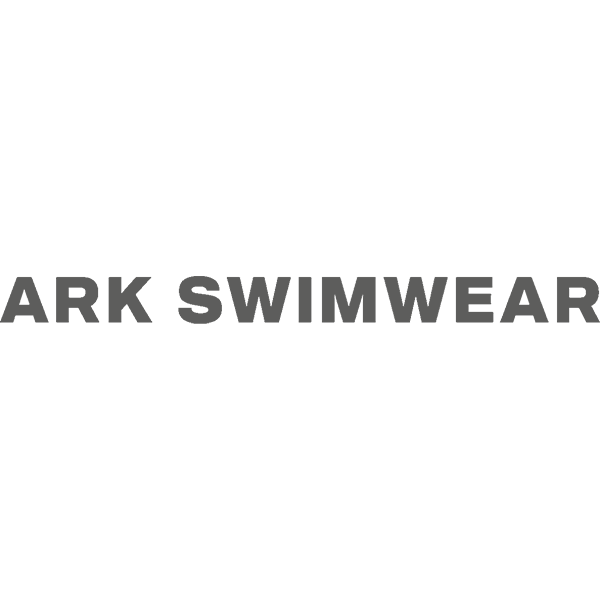
Ark Swimwear Streamlines Processes with Ramp and RFID
Retail, Inventory Tracking
Read now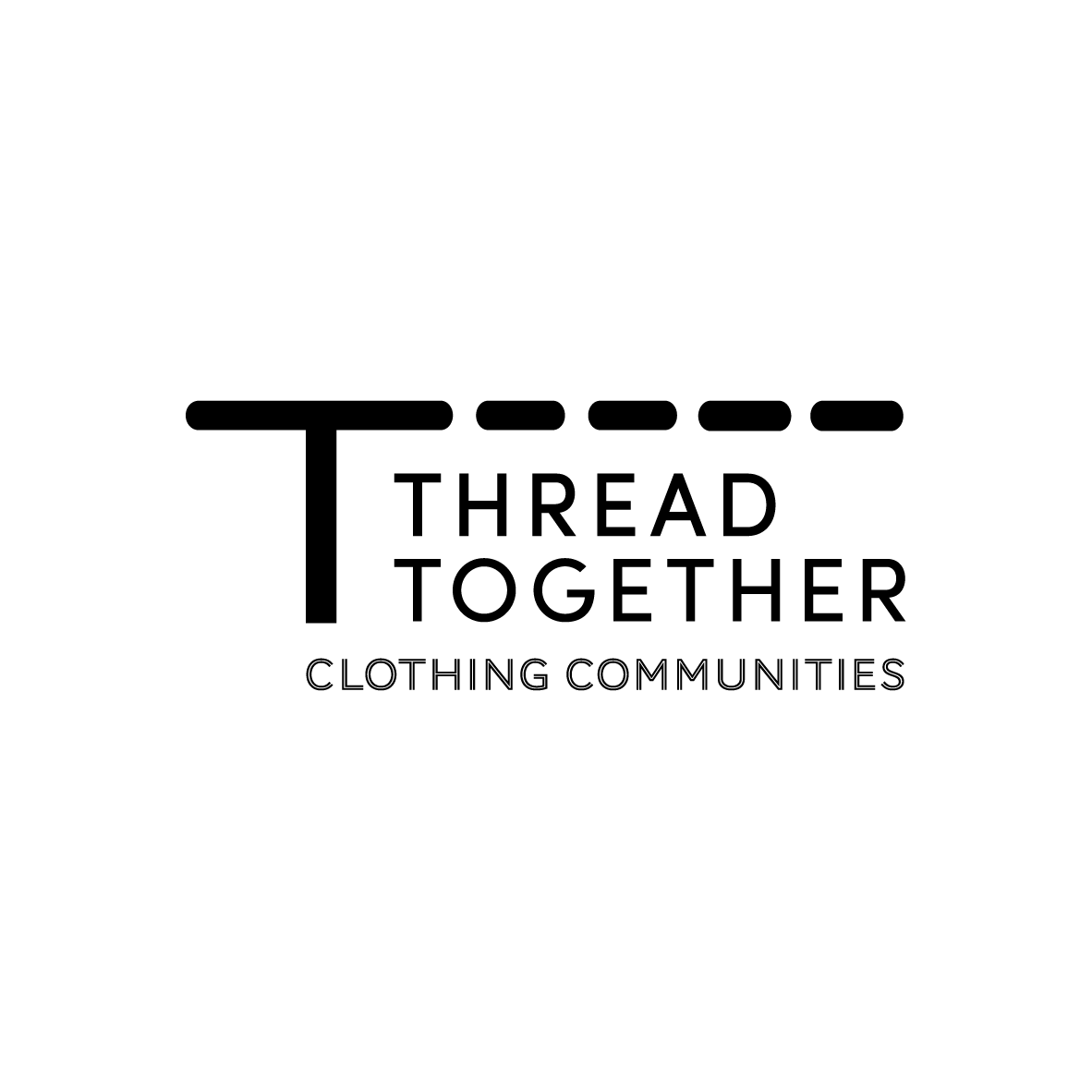
Innovating Charity: How RFID Technology is Transforming Thread Together
Retail, Inventory Tracking
Read now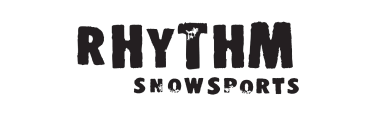
Rhythm Snowports conquering Inventory Challenges with Ramp’s RFID solution.
Retail, Inventory Tracking
Read nowLeading brands thriving with RAMP RFID solutions
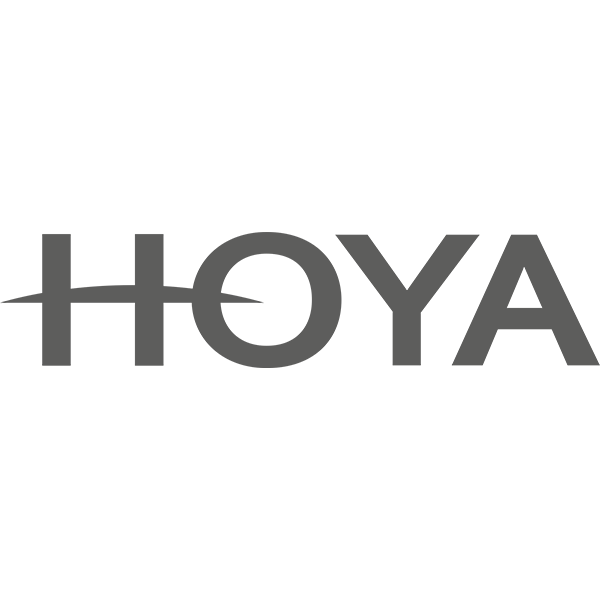
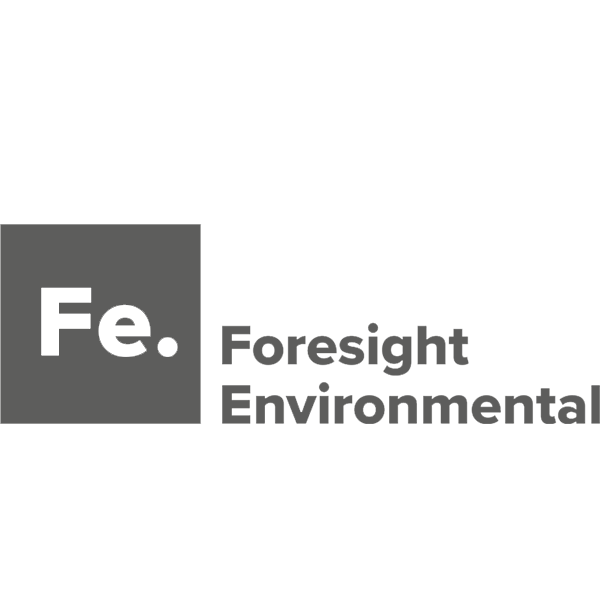

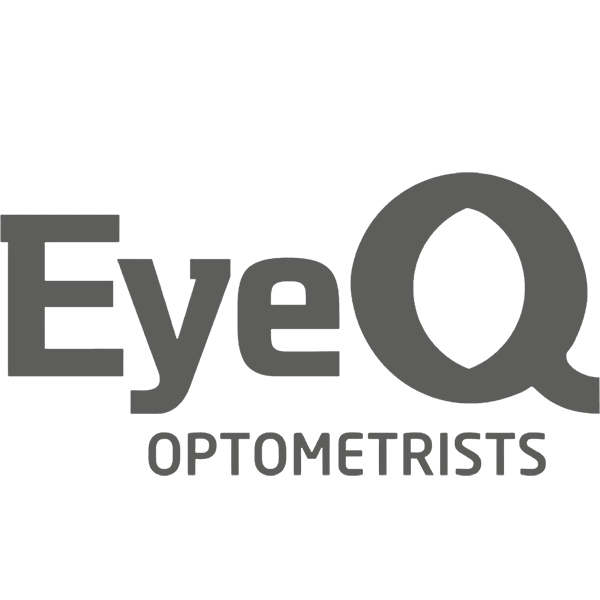
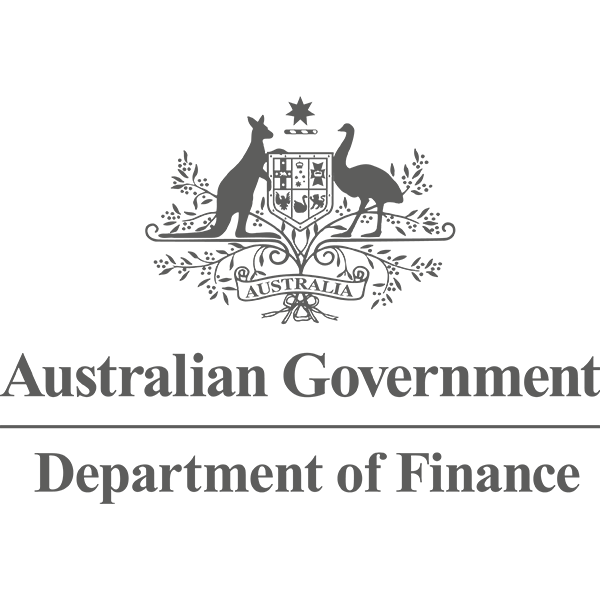
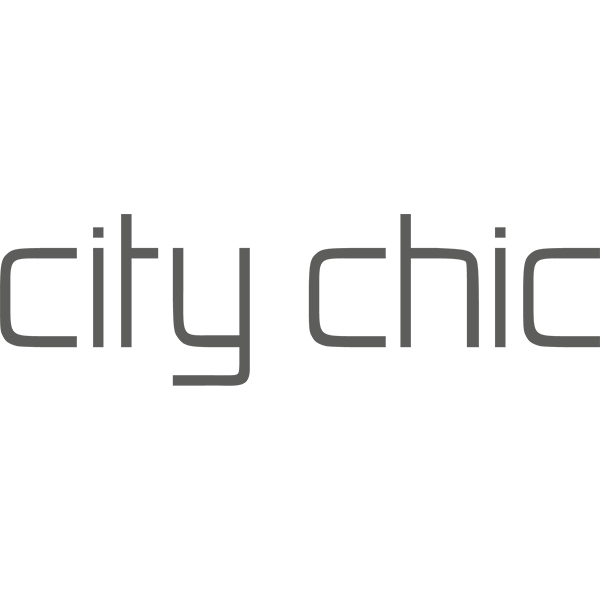
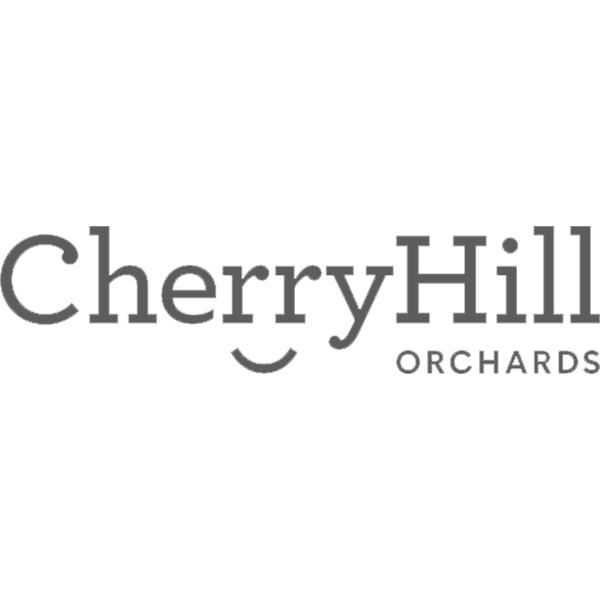
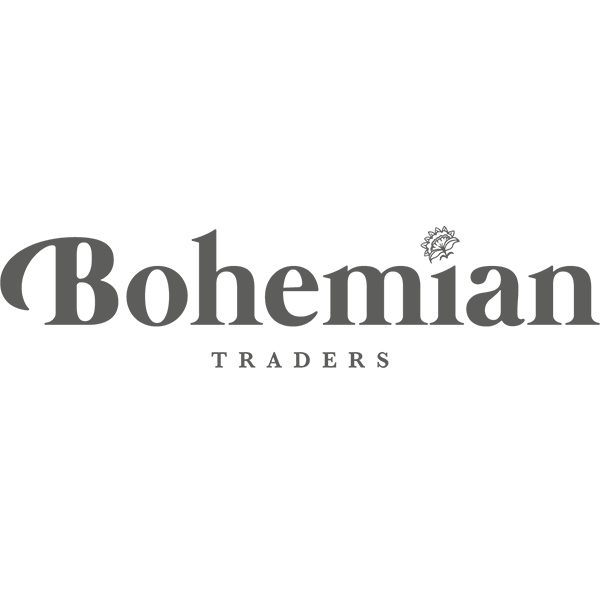
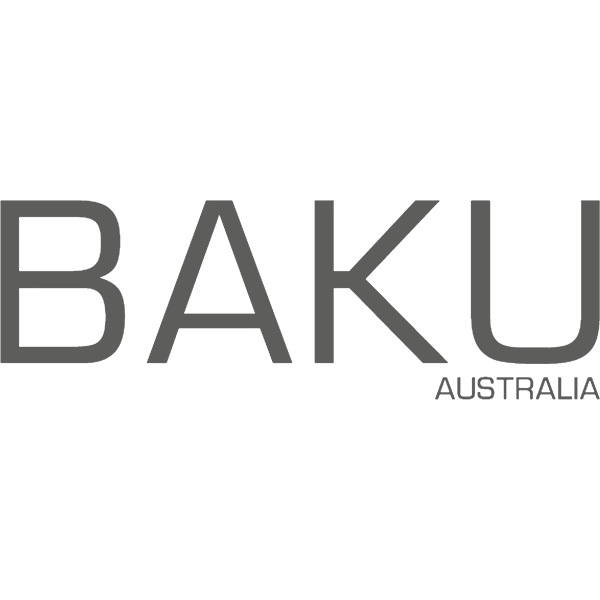
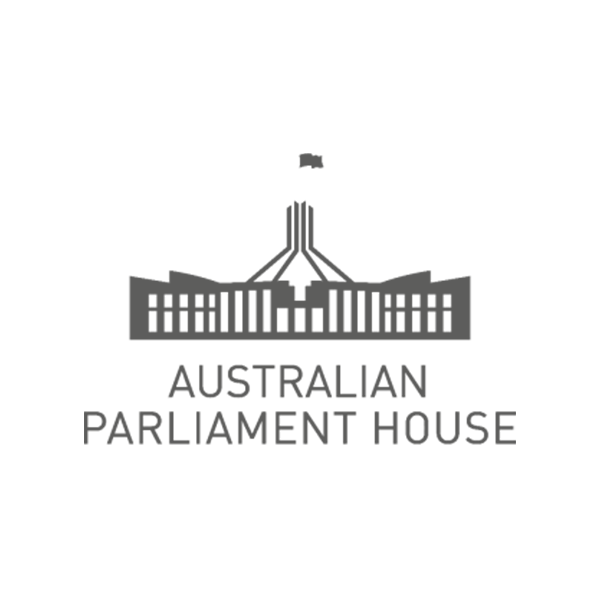
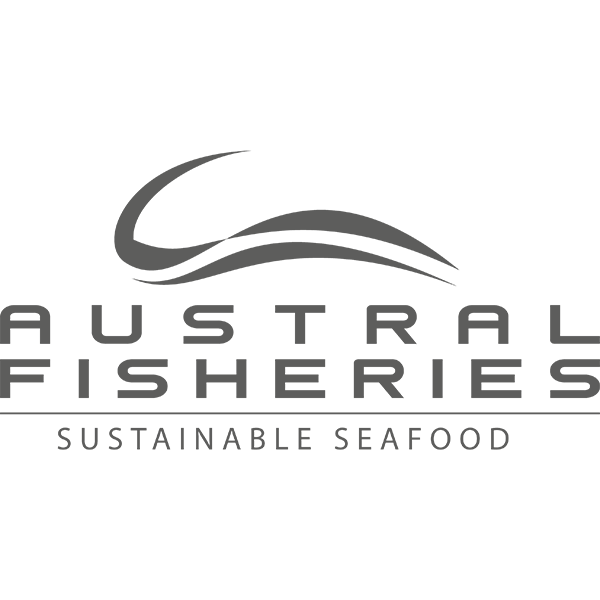
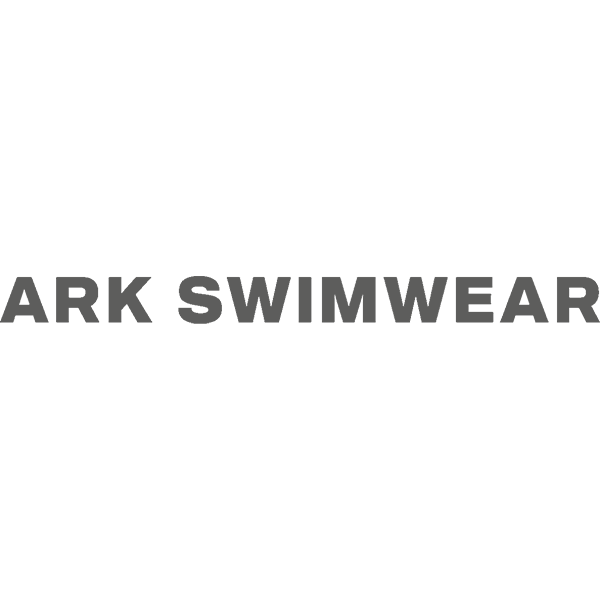
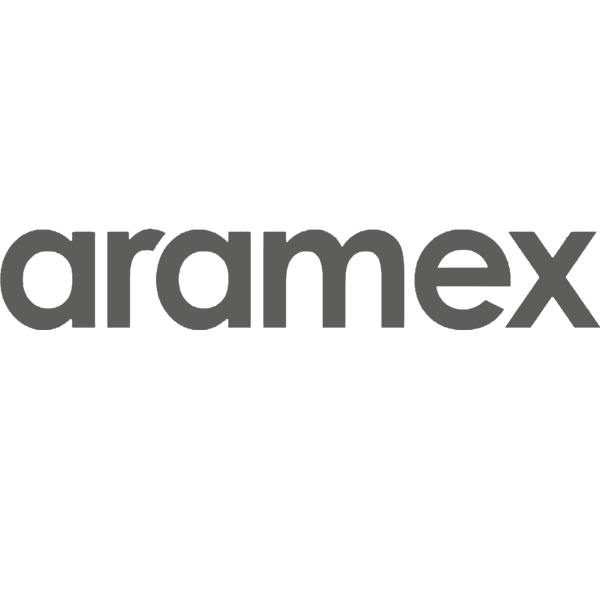
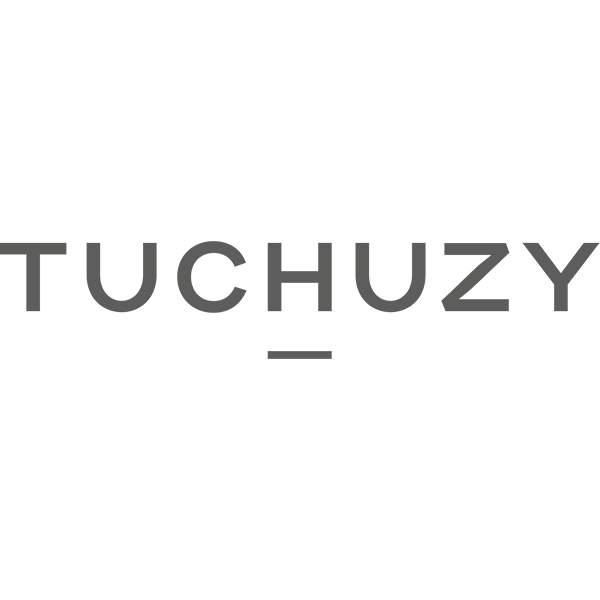
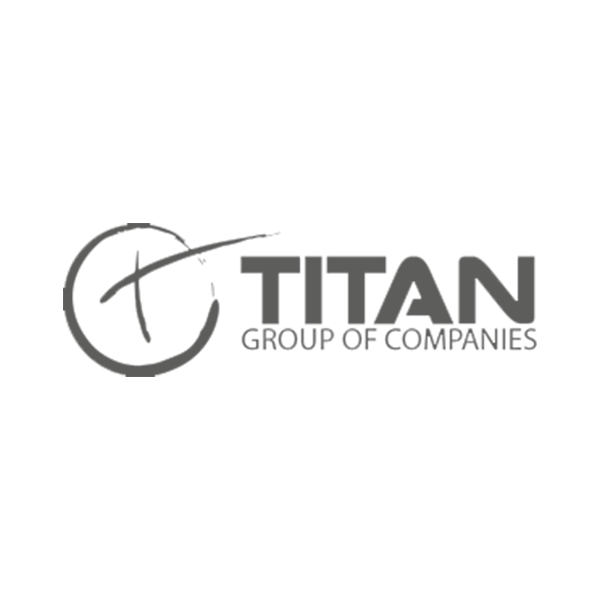
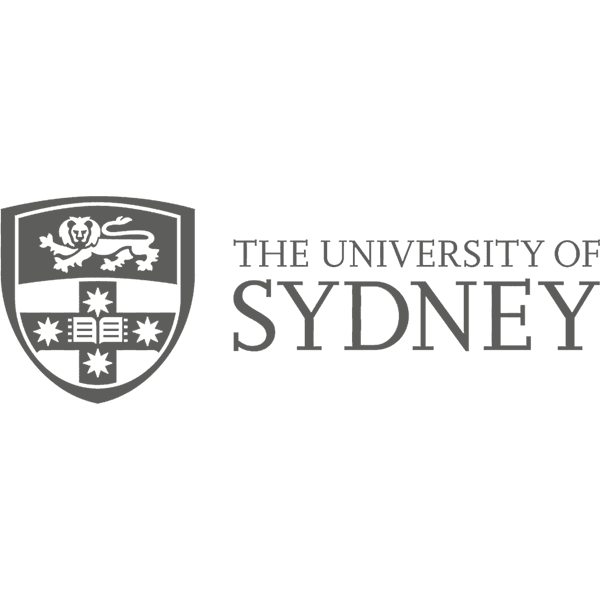
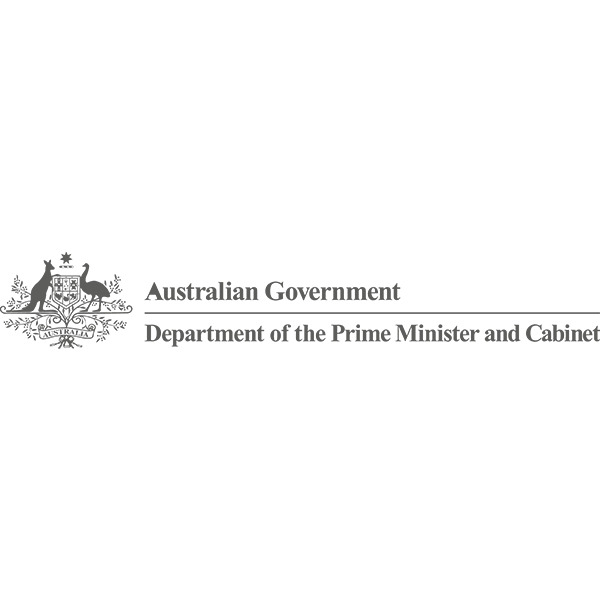
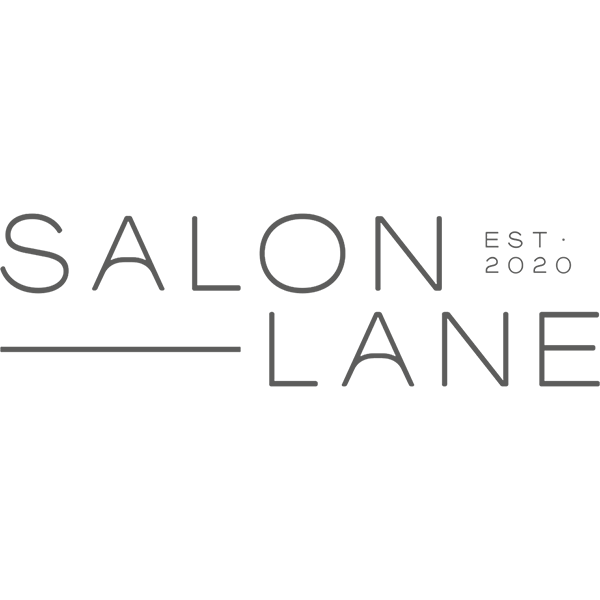
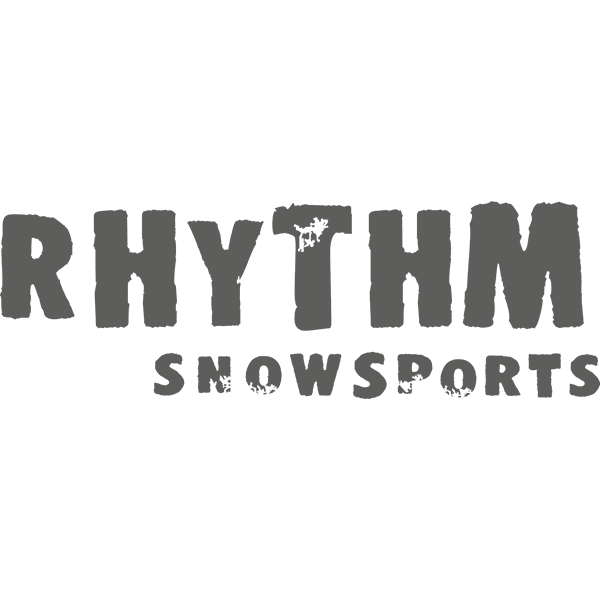
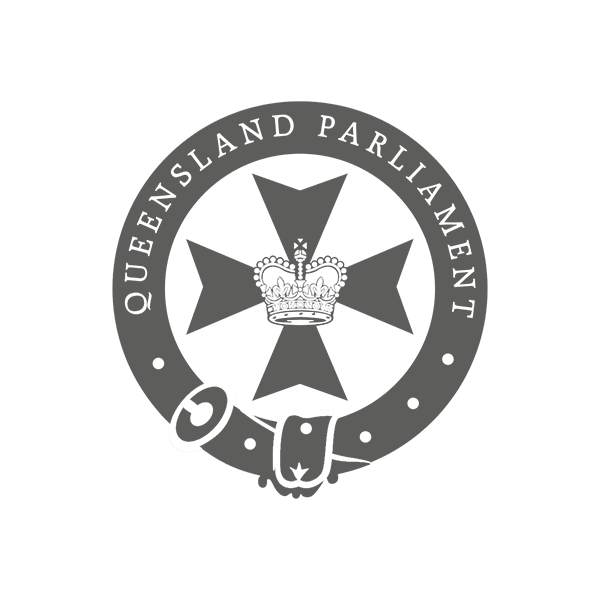
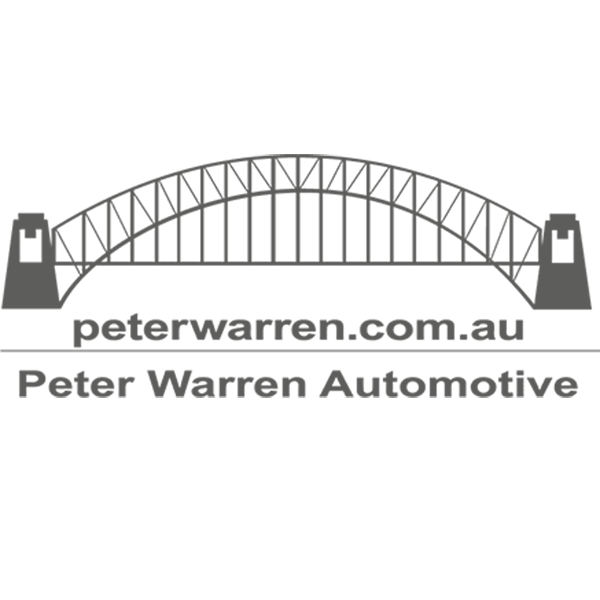
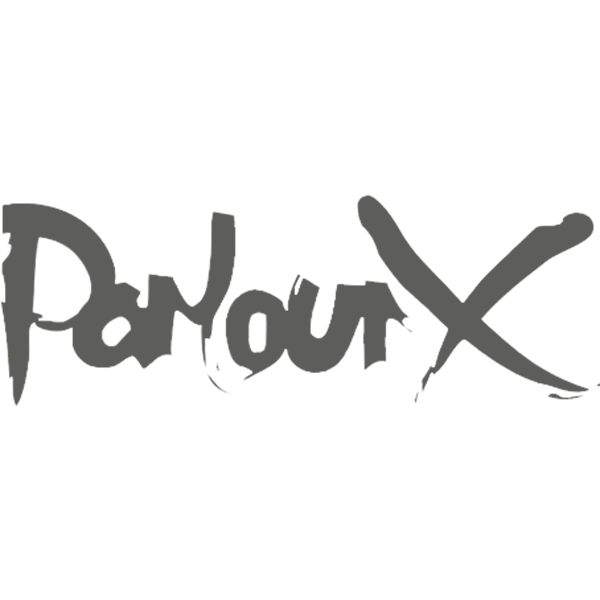
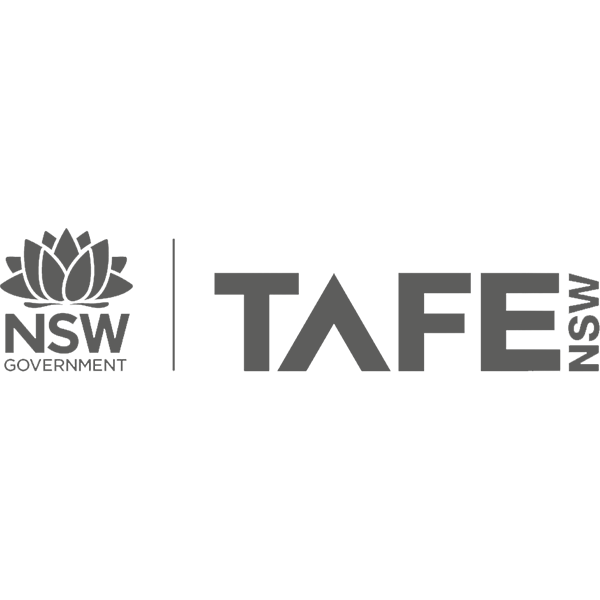
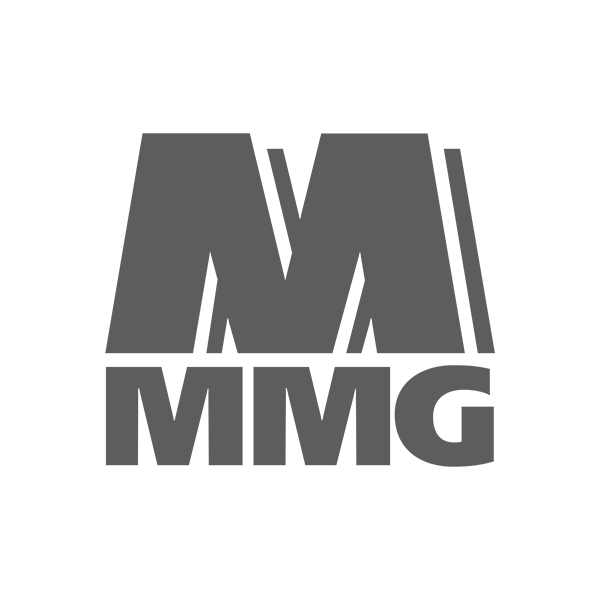
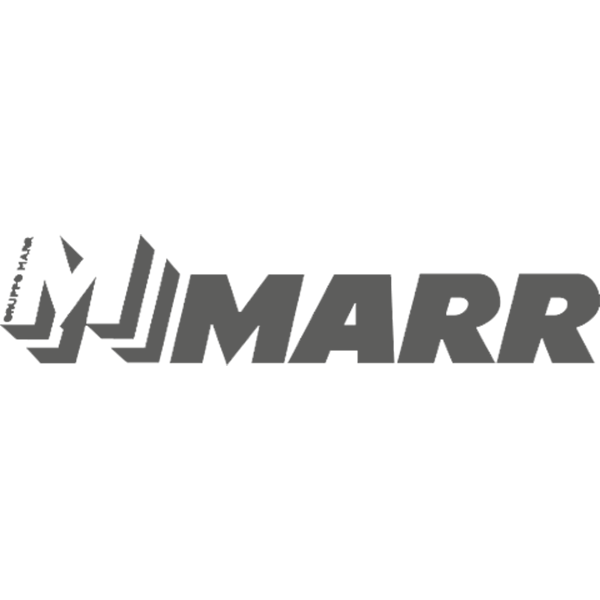
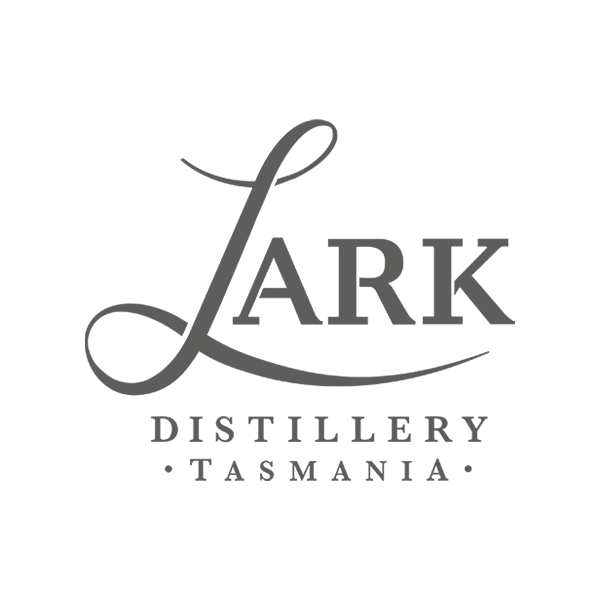
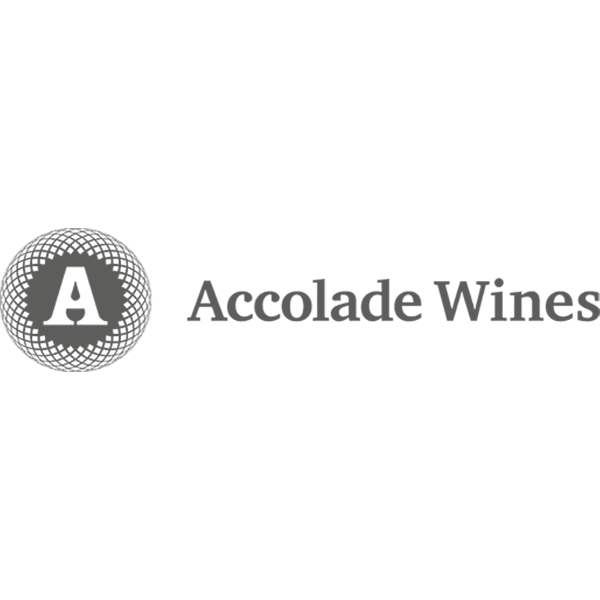
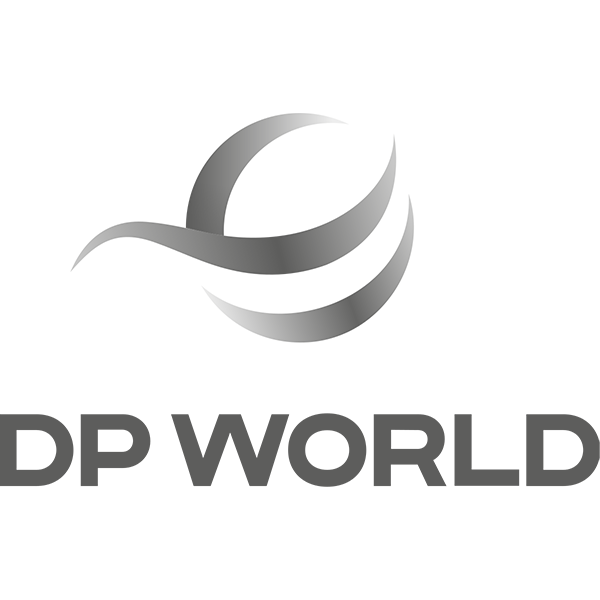
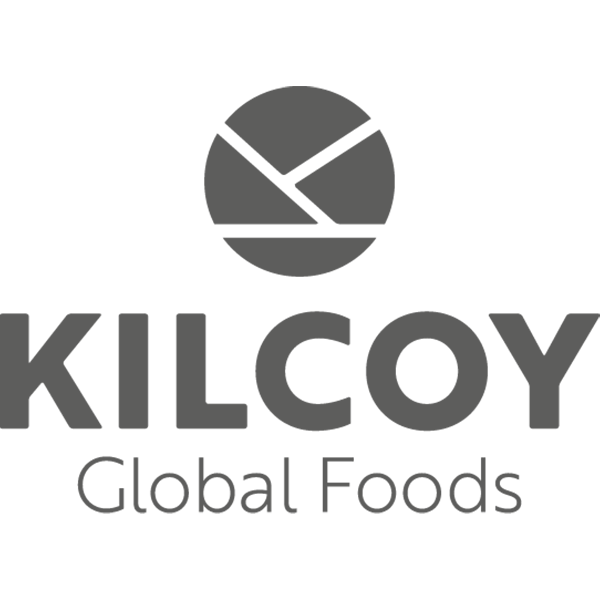
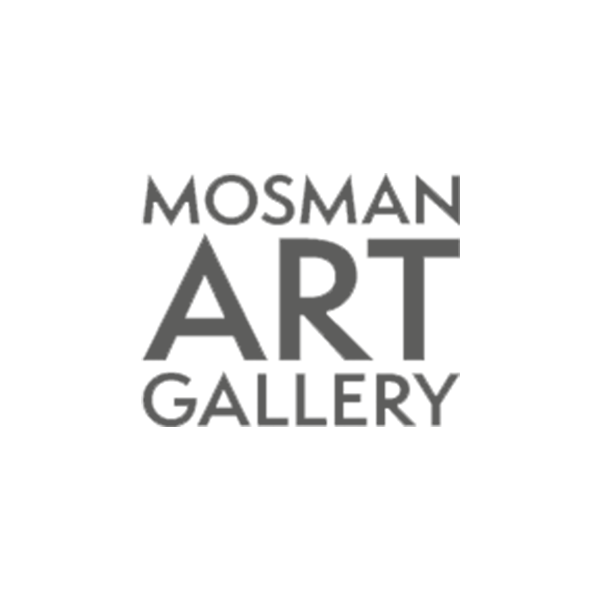
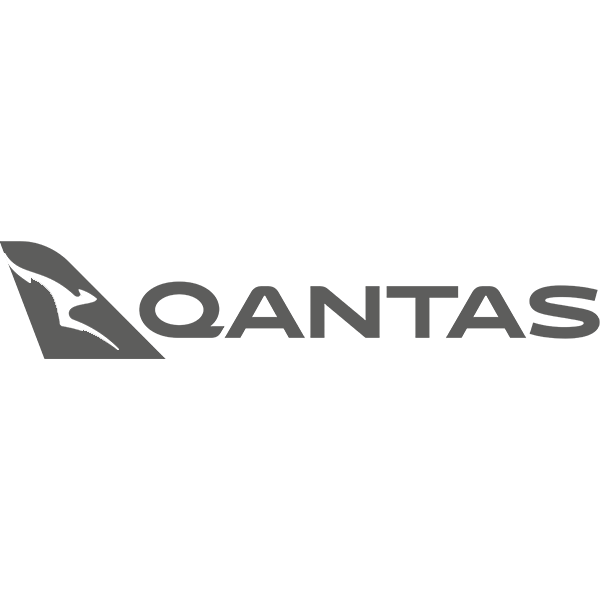
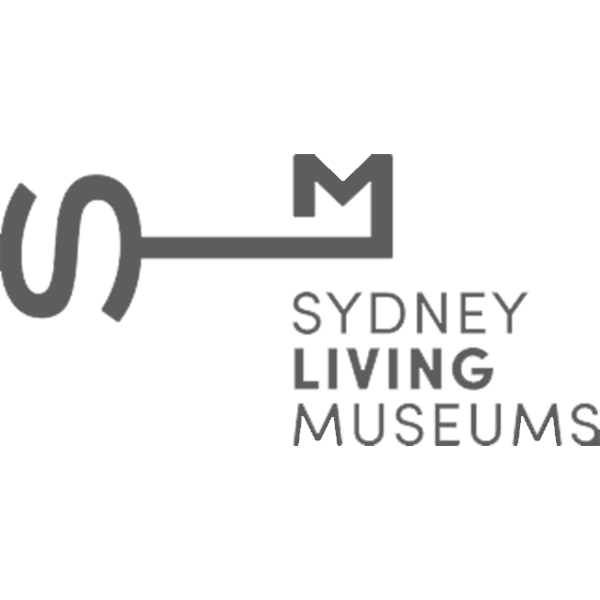
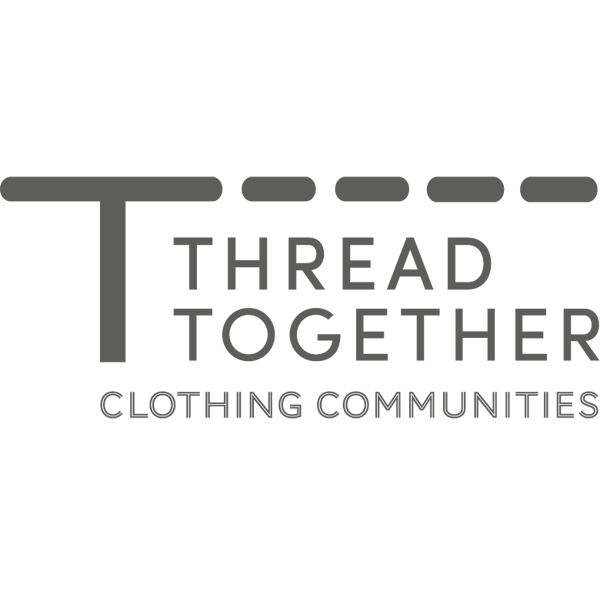
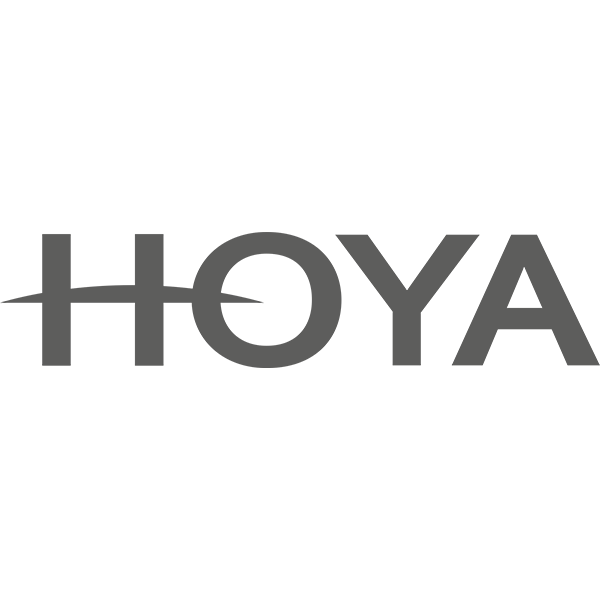
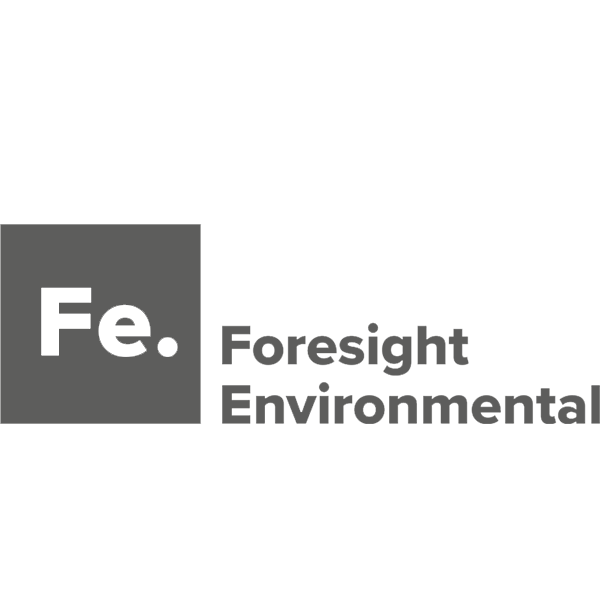

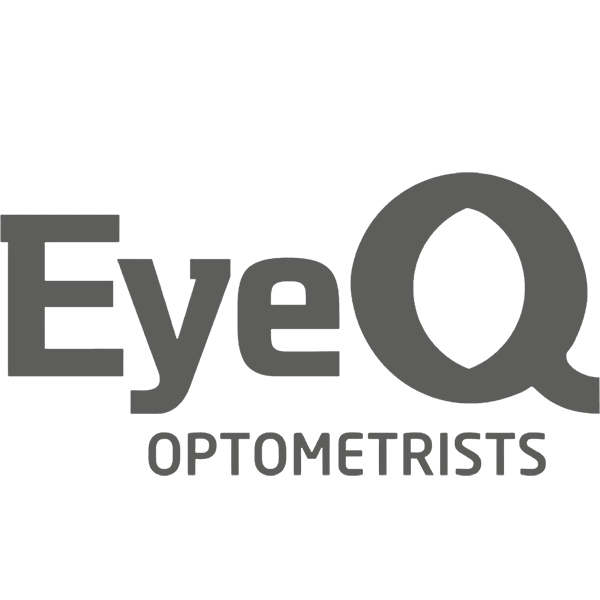
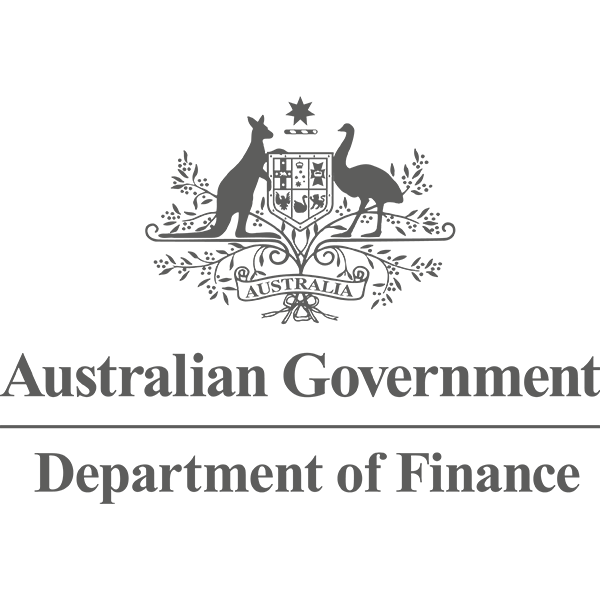
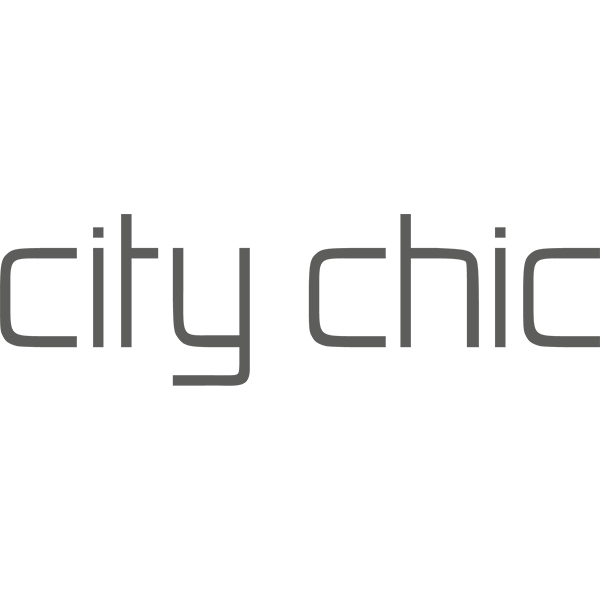
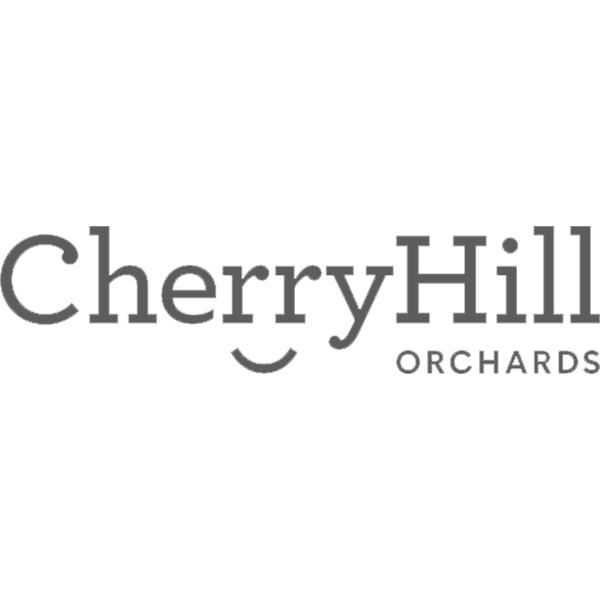
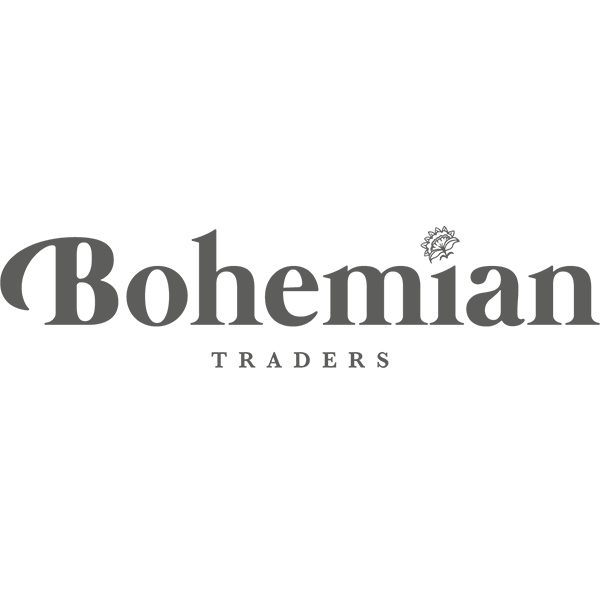
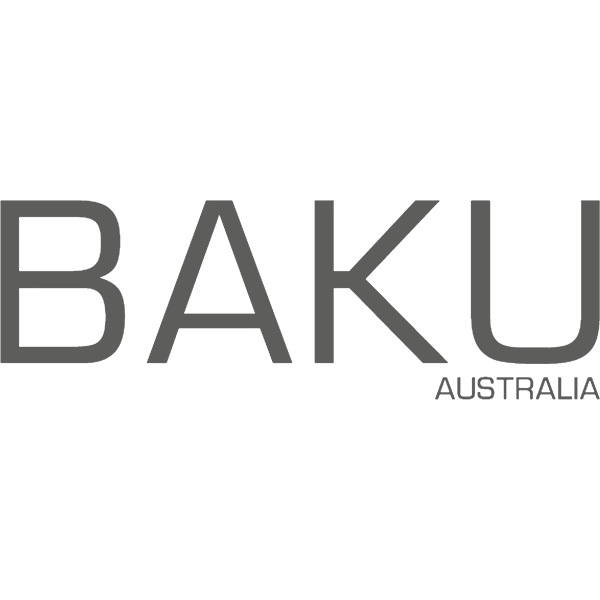
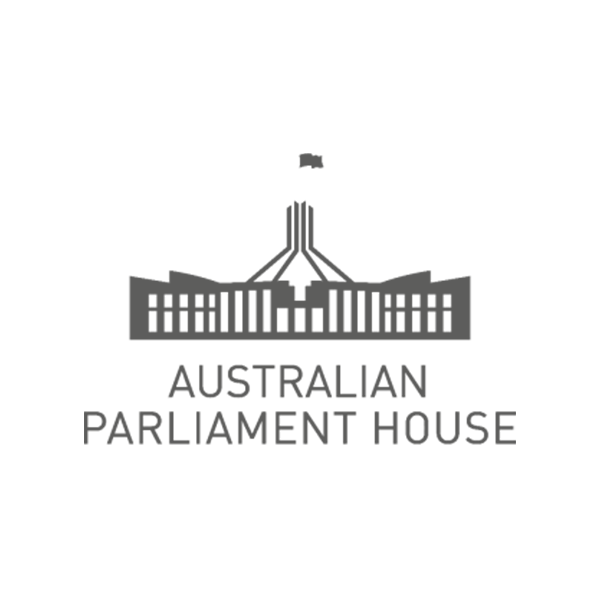
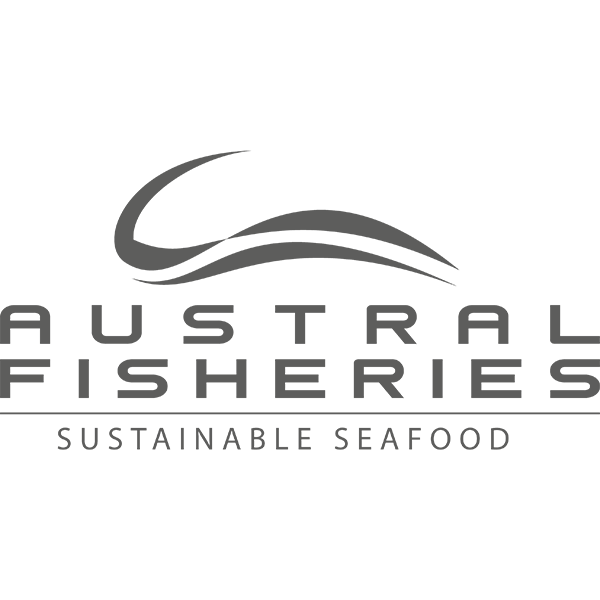
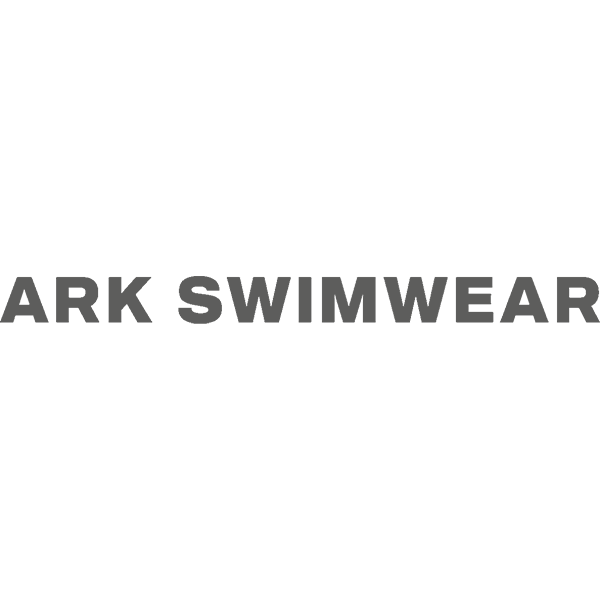
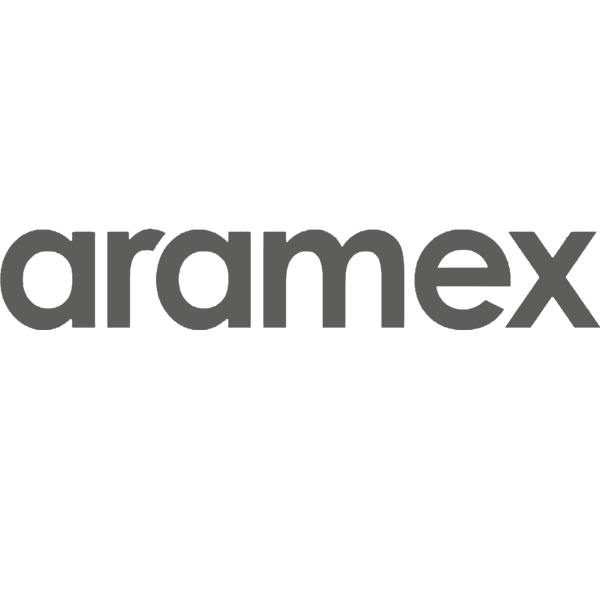
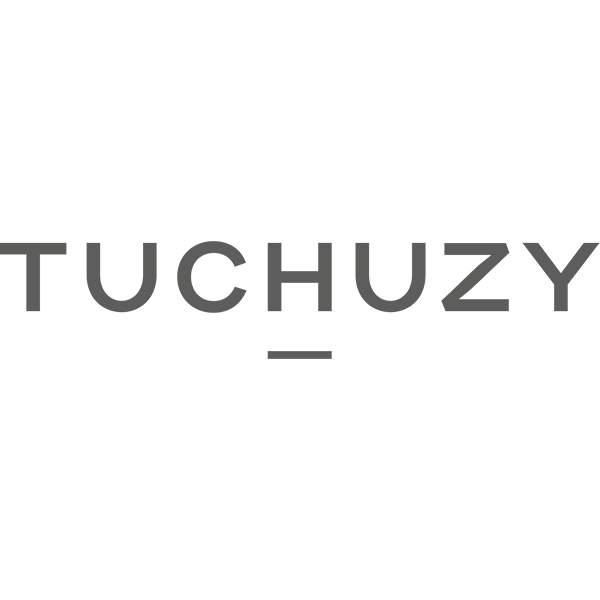
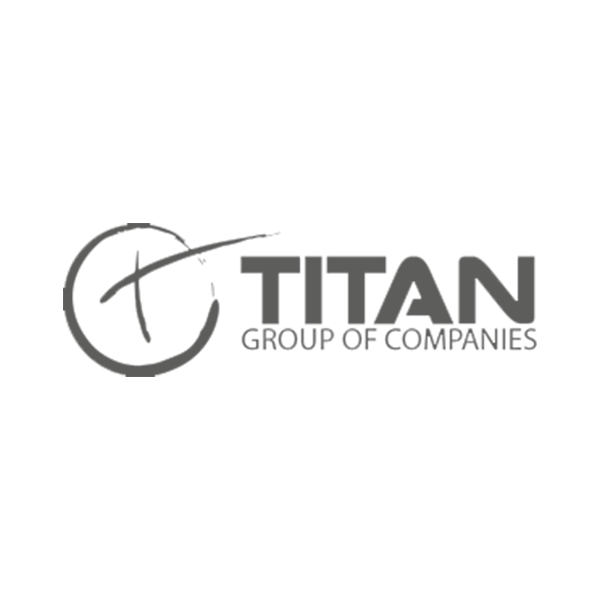
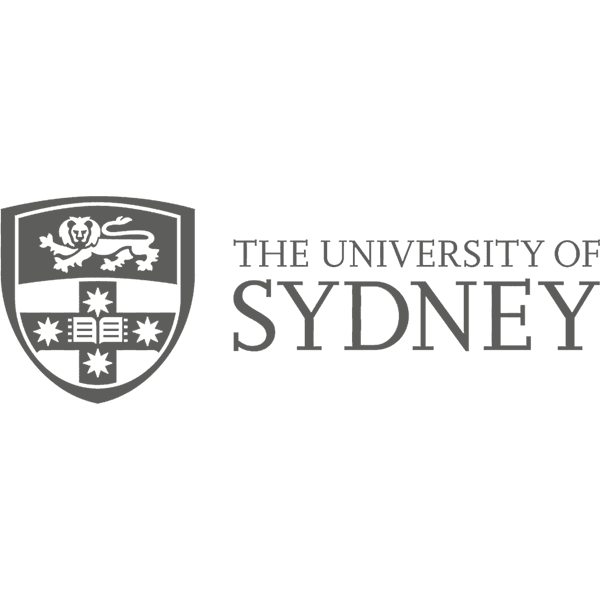
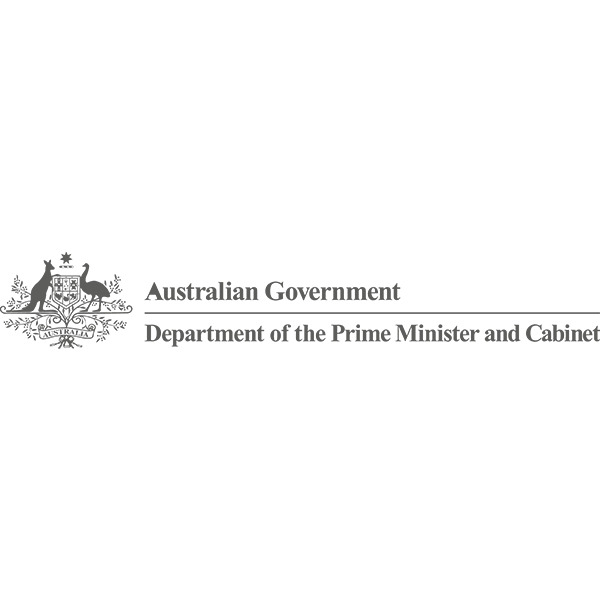
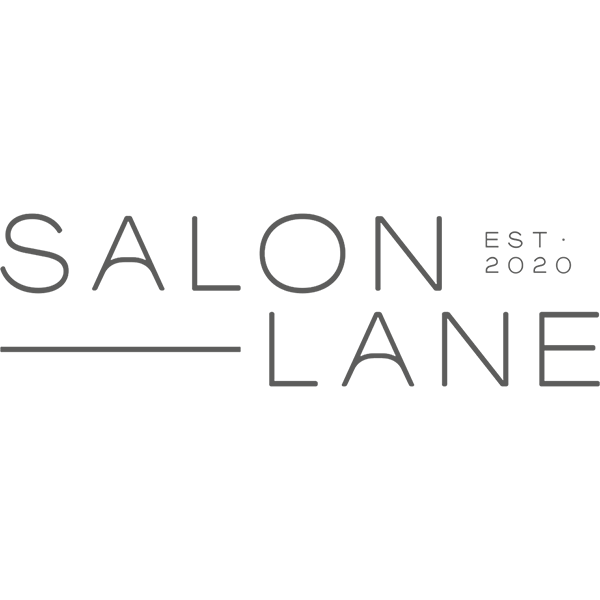
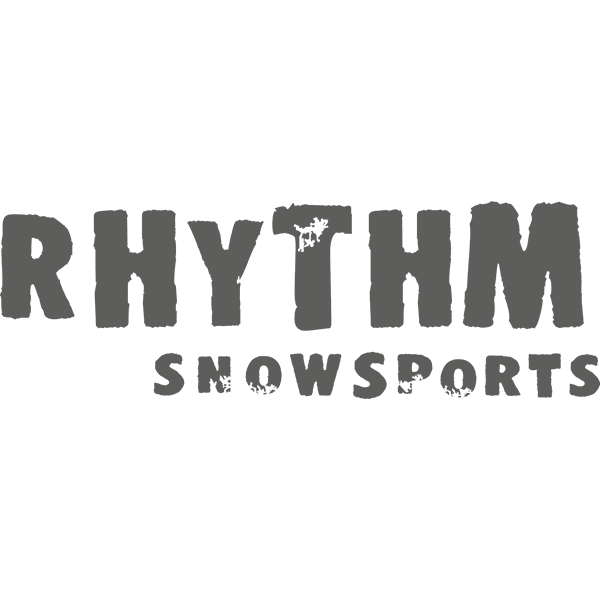
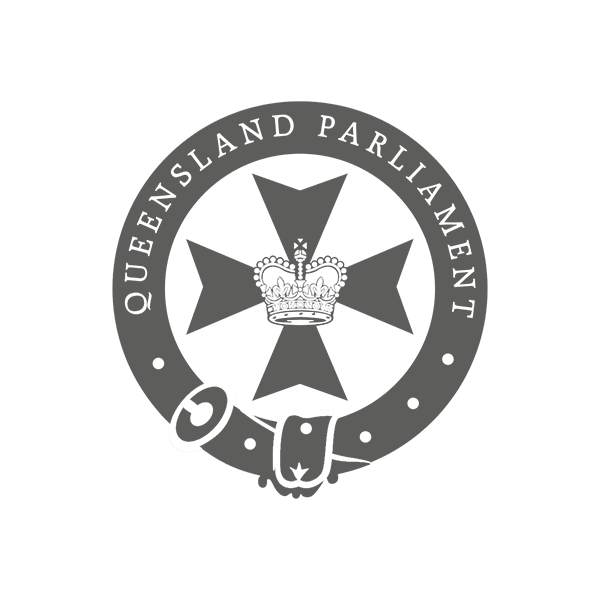
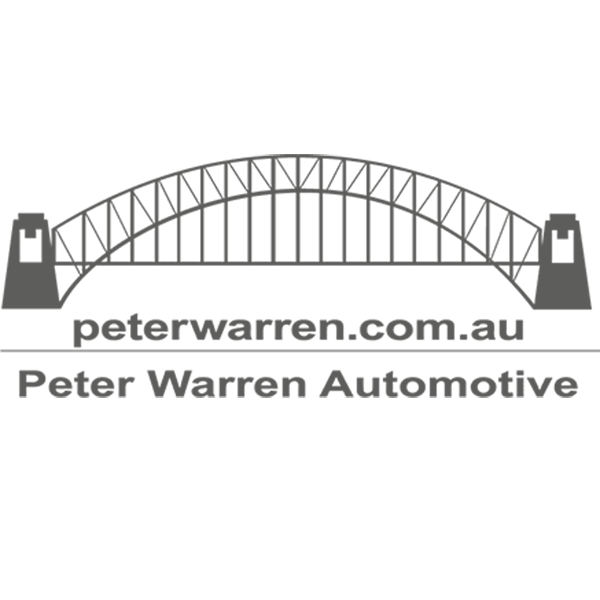
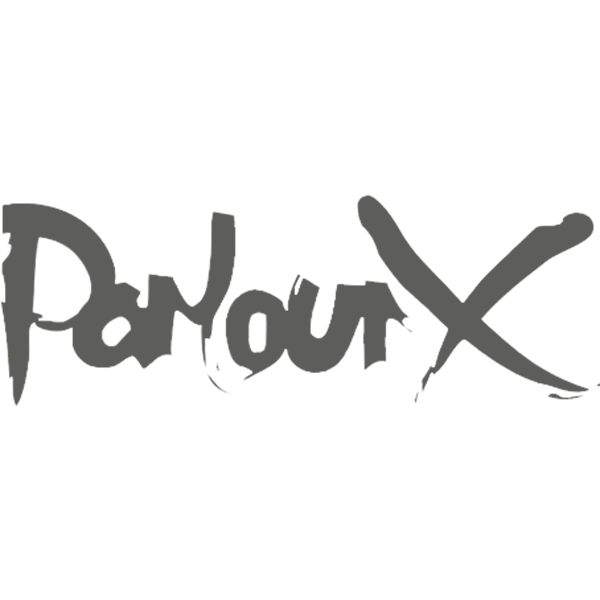
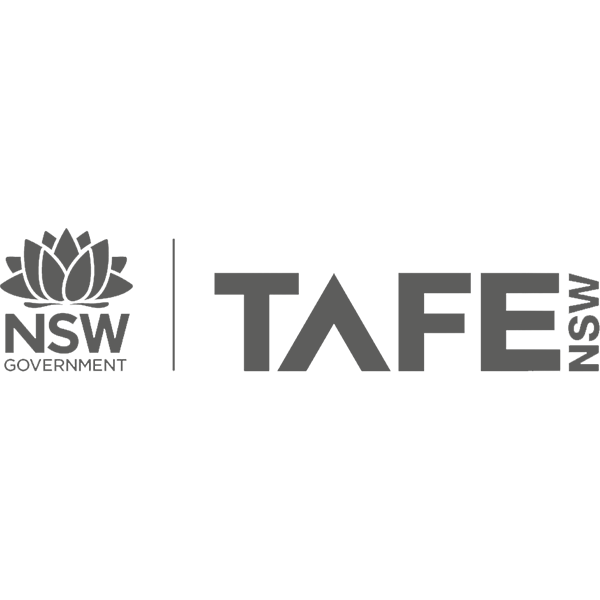
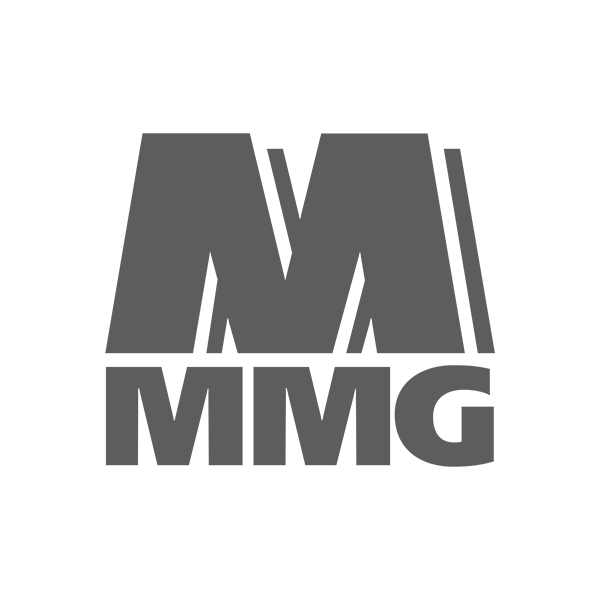
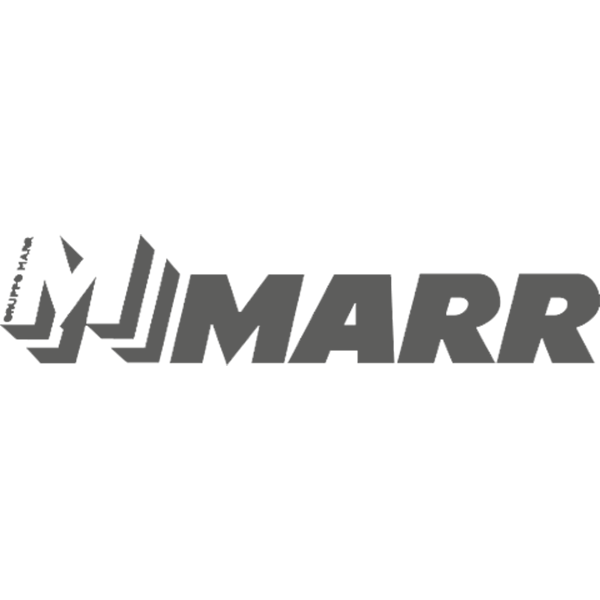
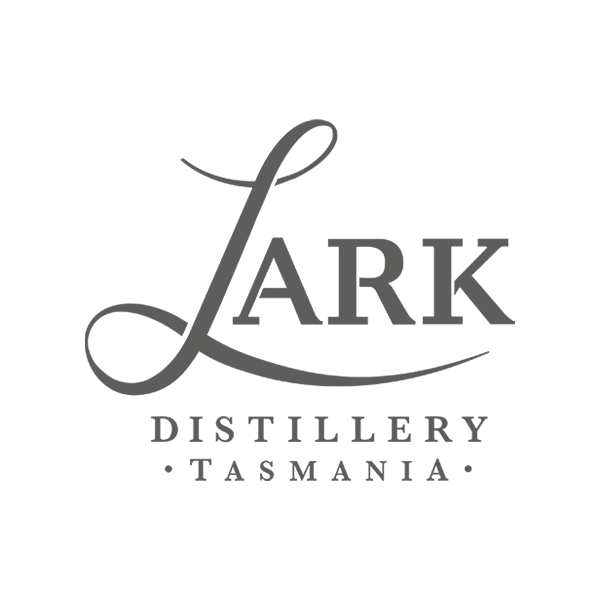
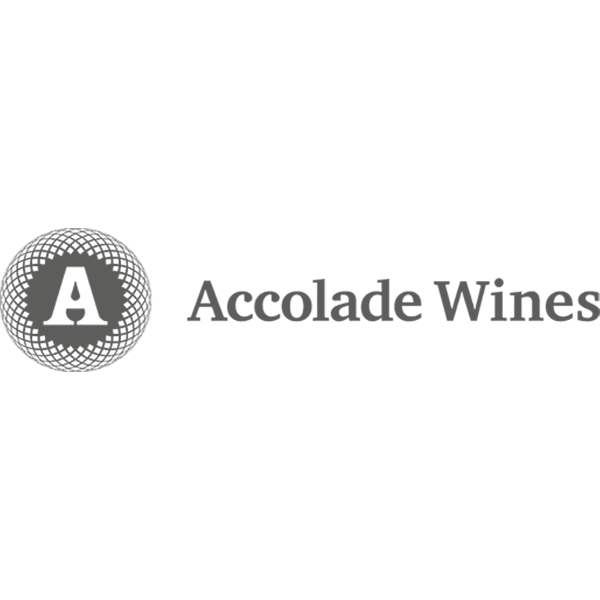
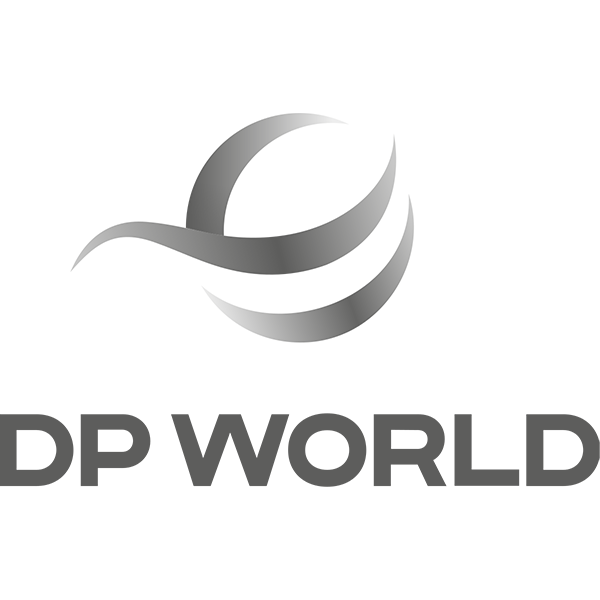
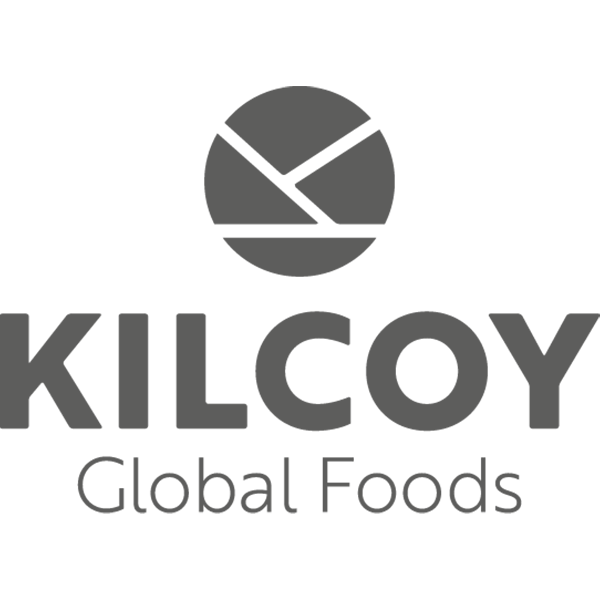
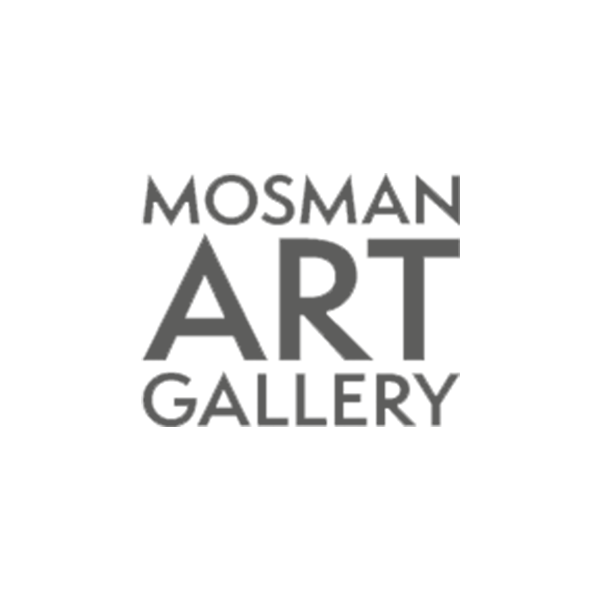
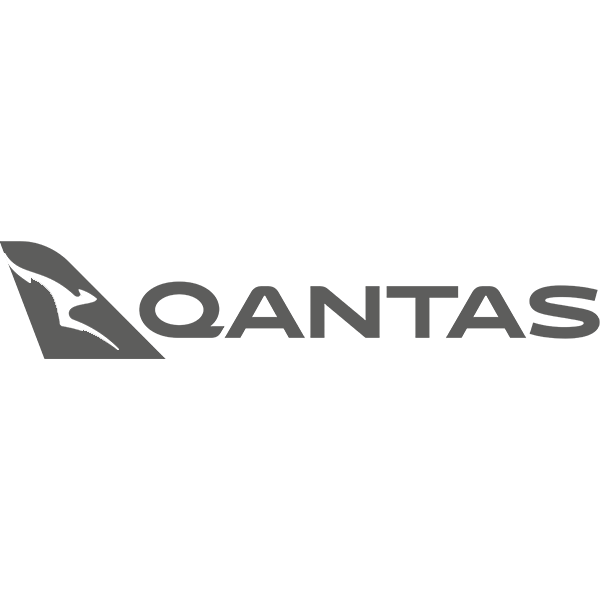
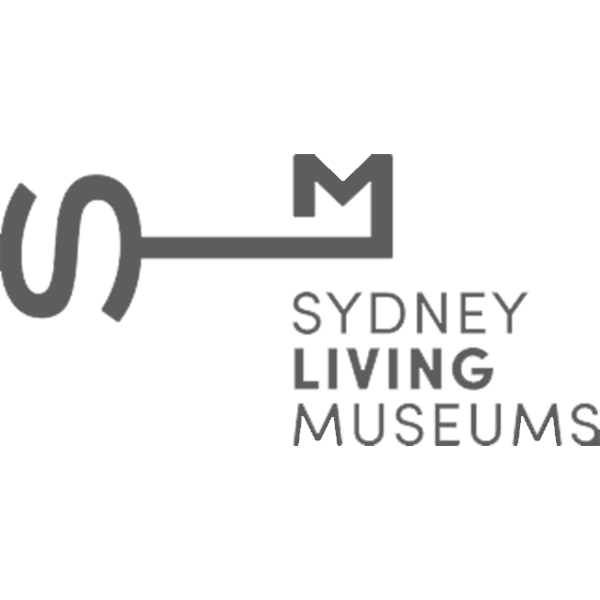
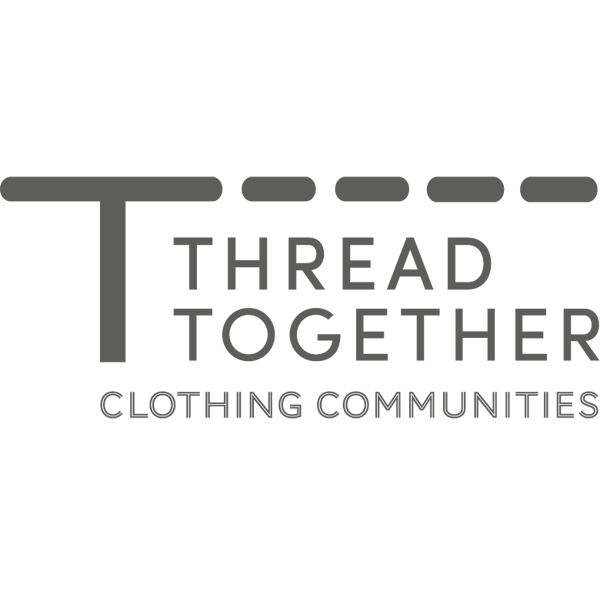
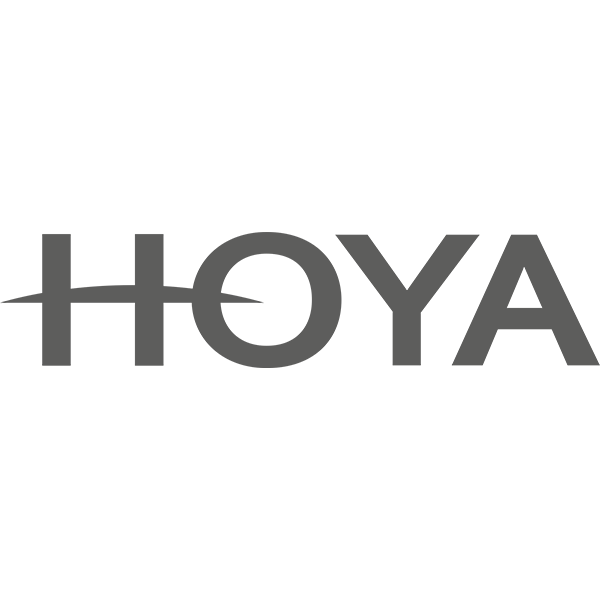
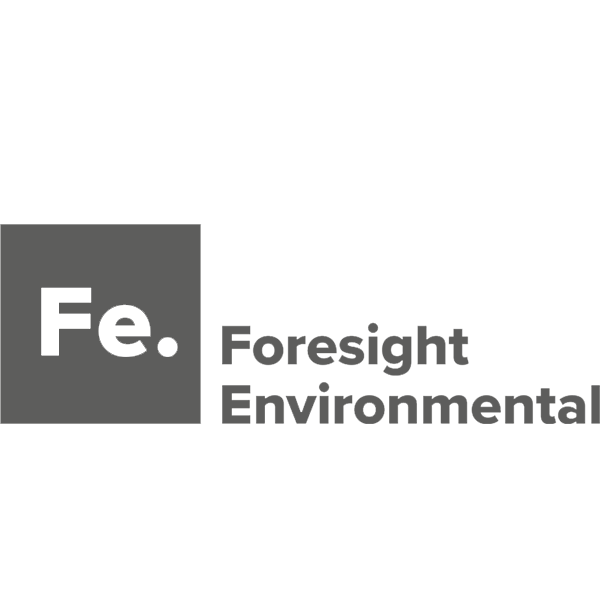

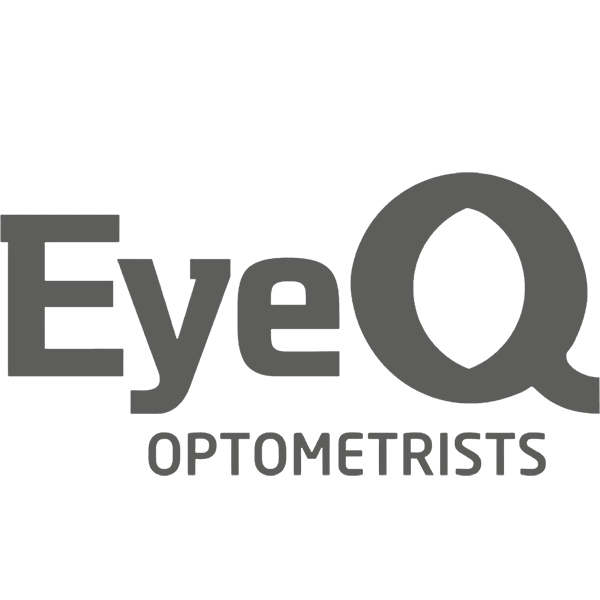
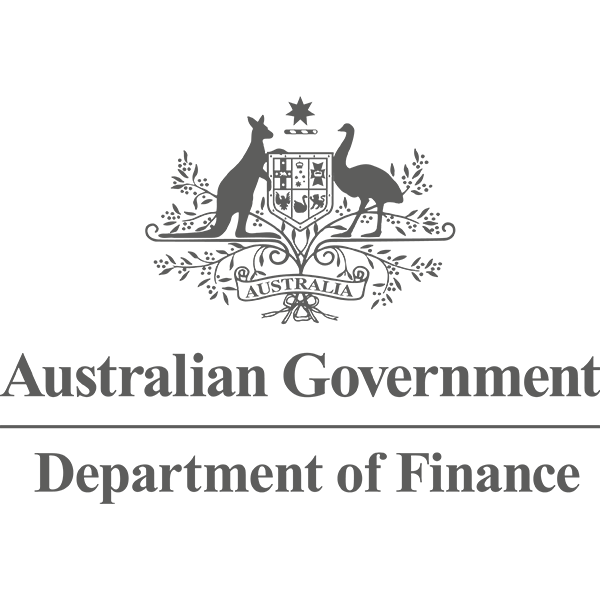
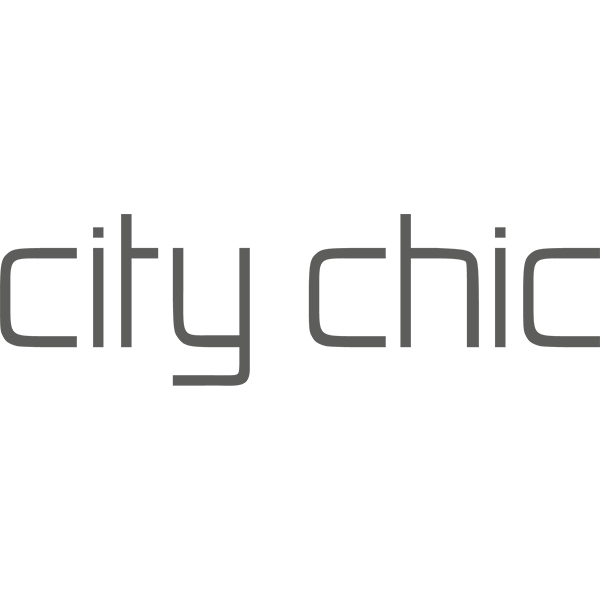
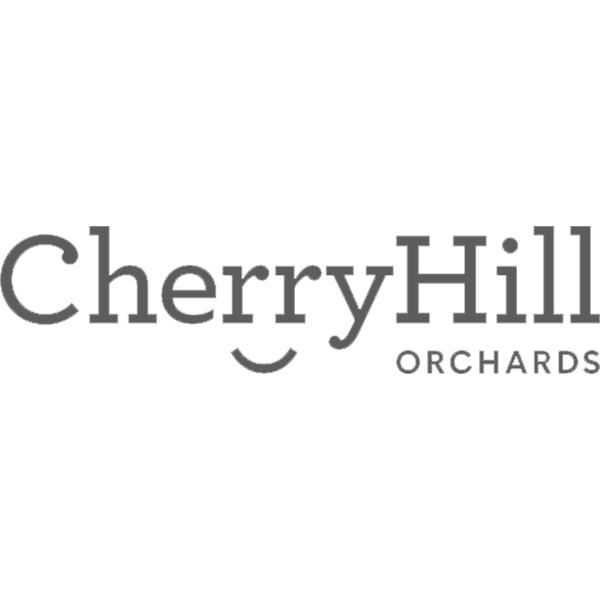
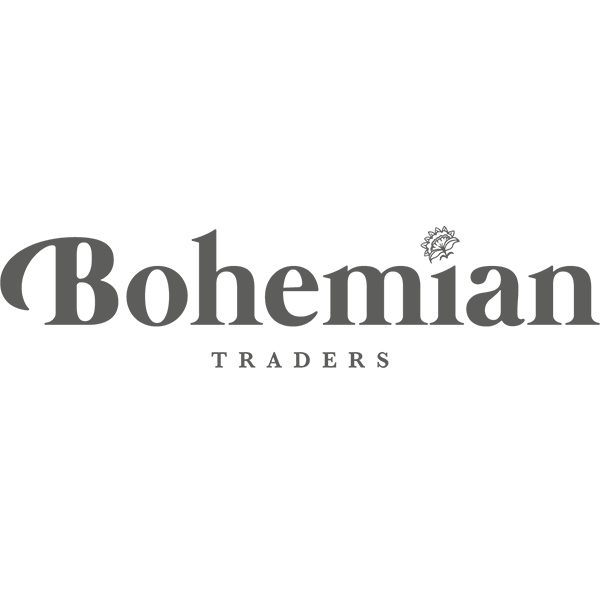
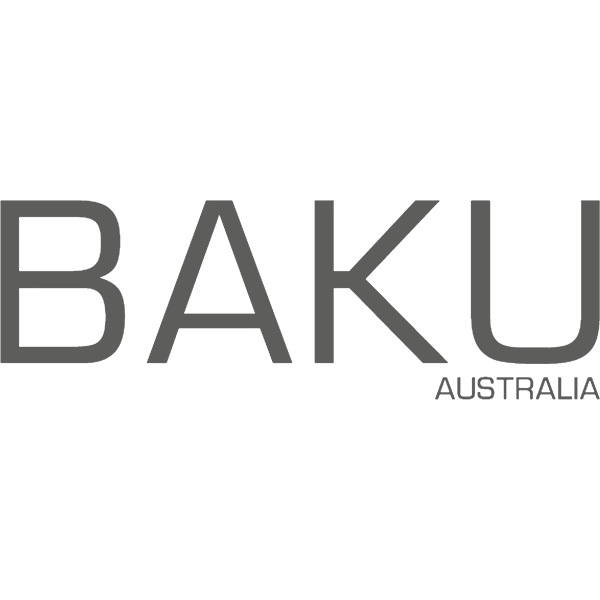
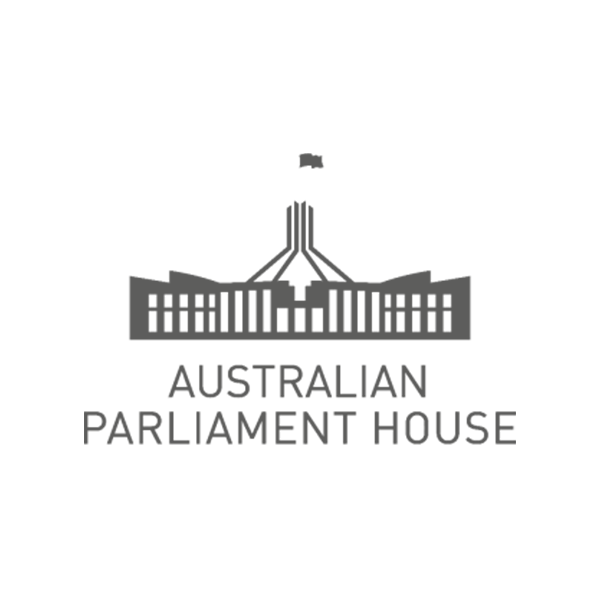
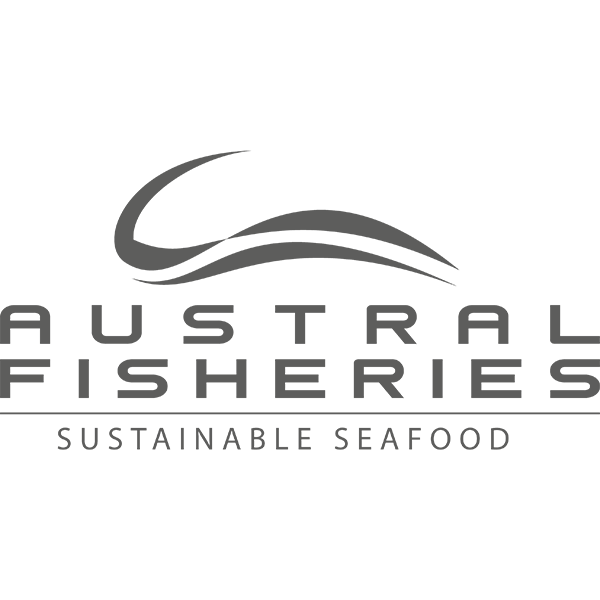
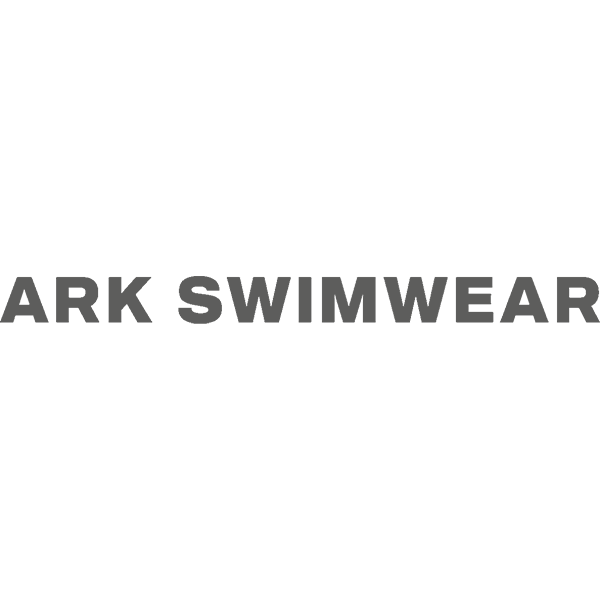
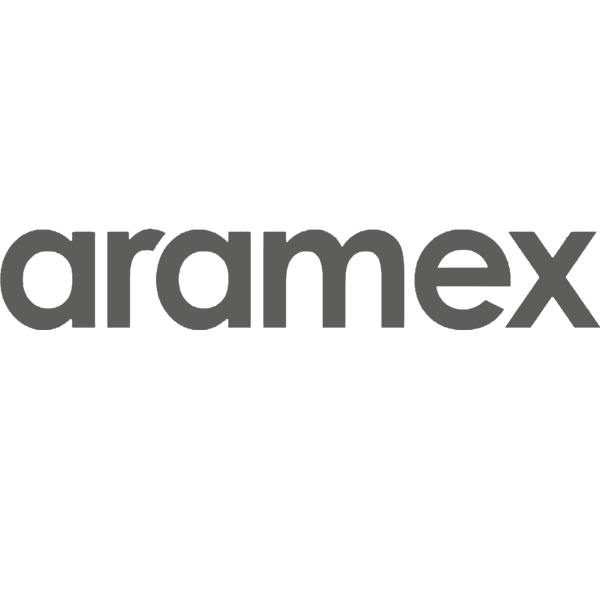
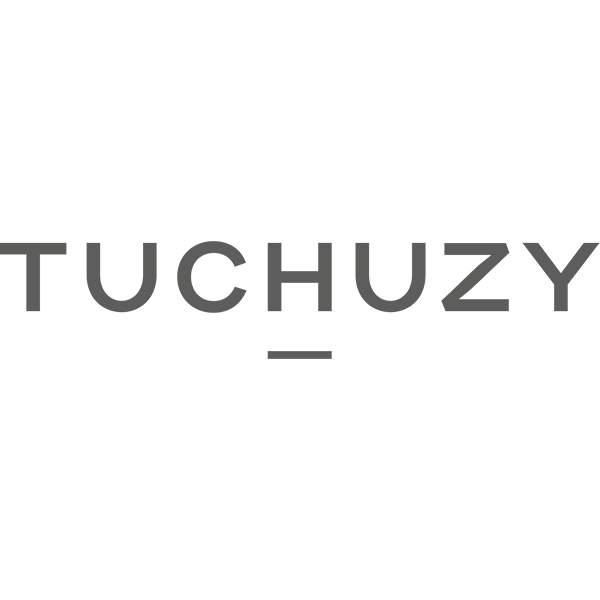
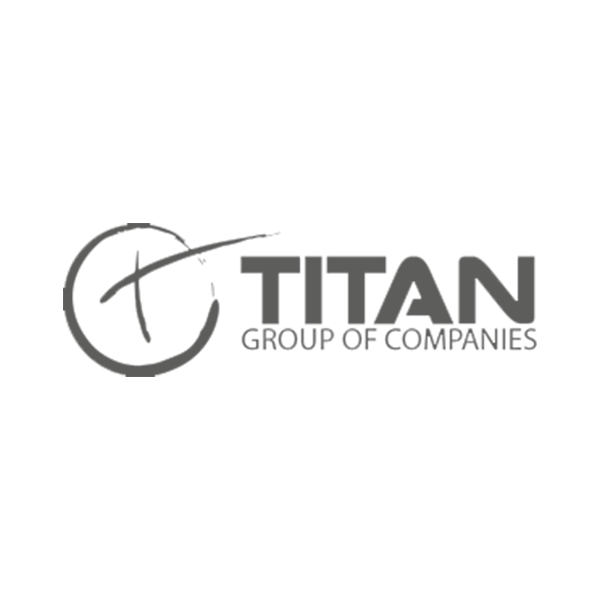
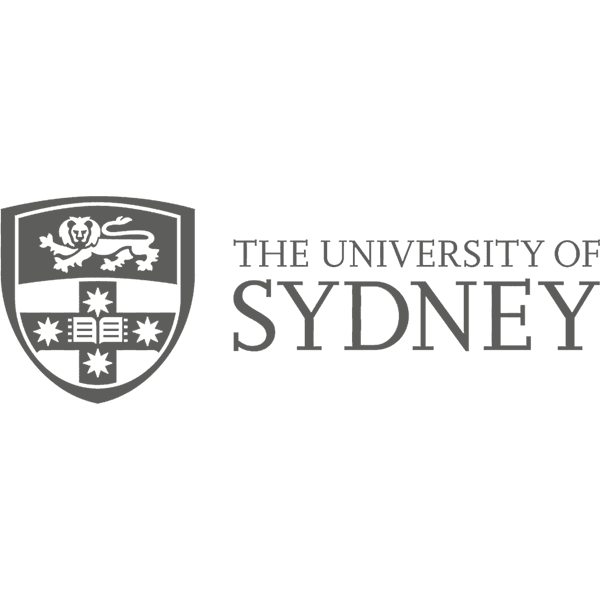
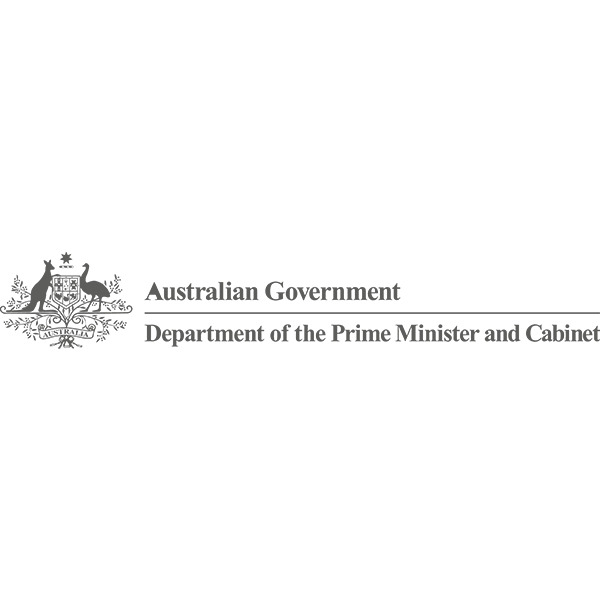
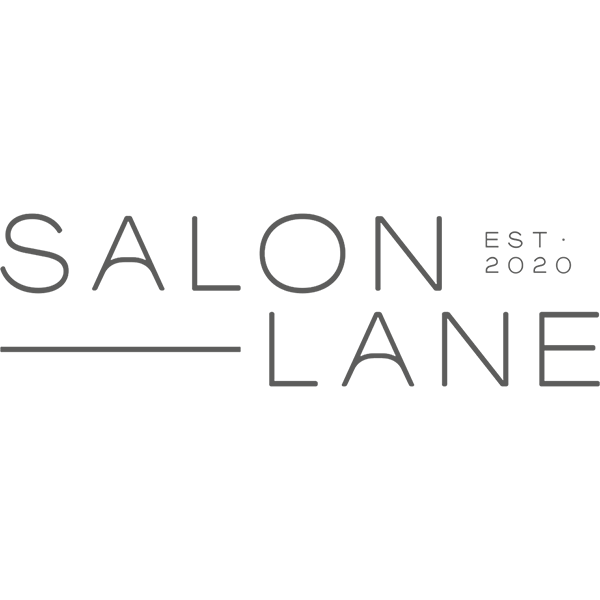
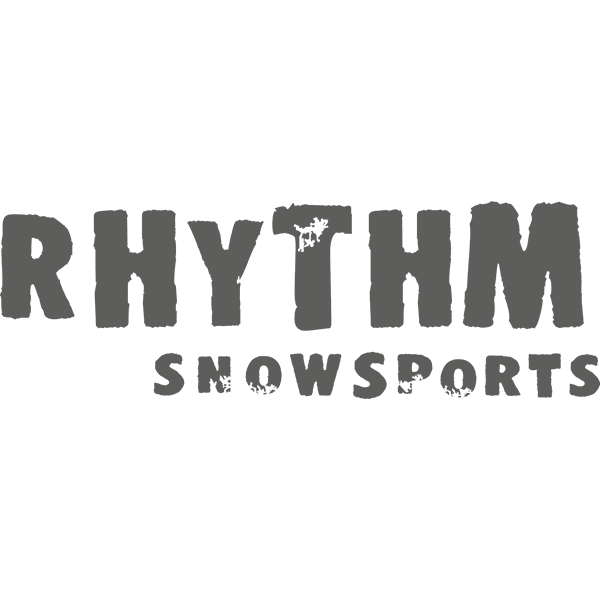
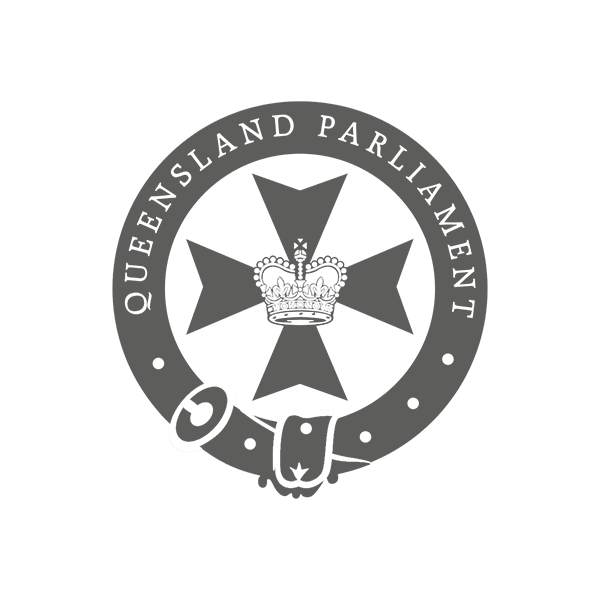
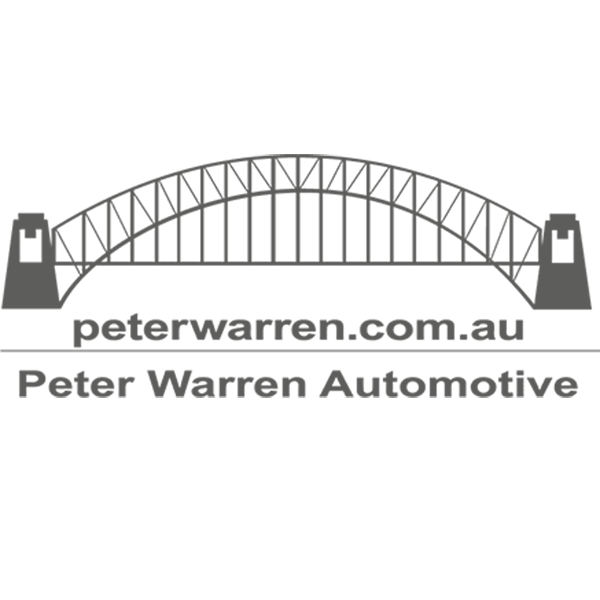
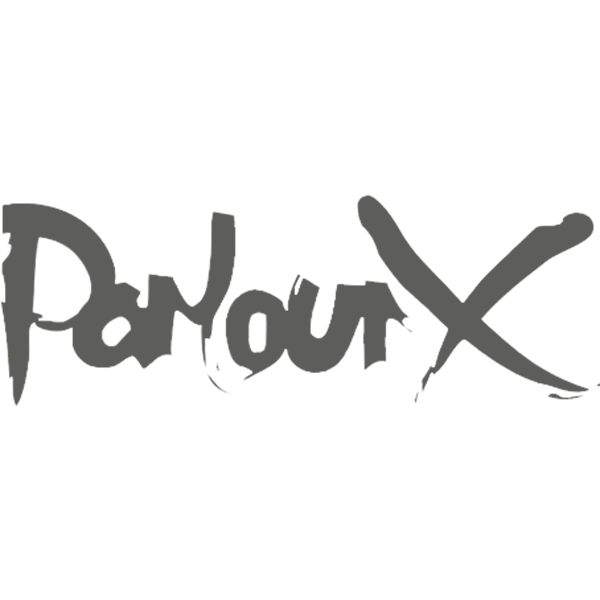
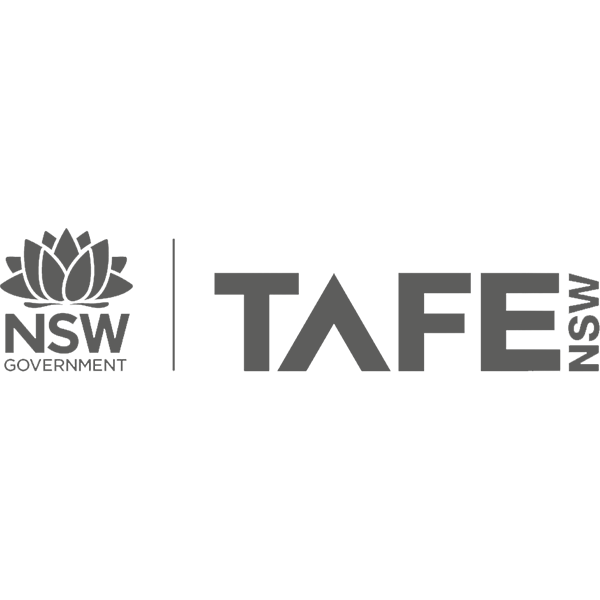
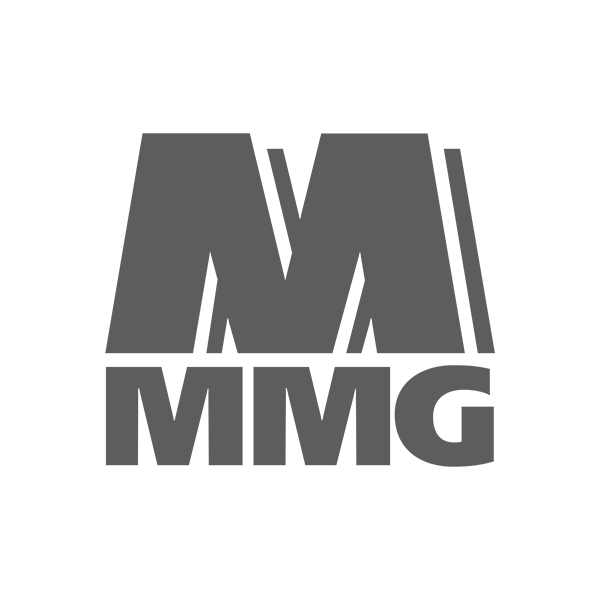
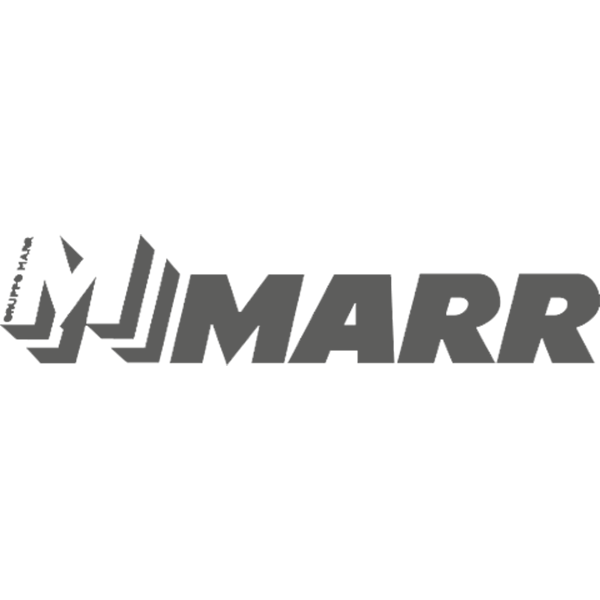
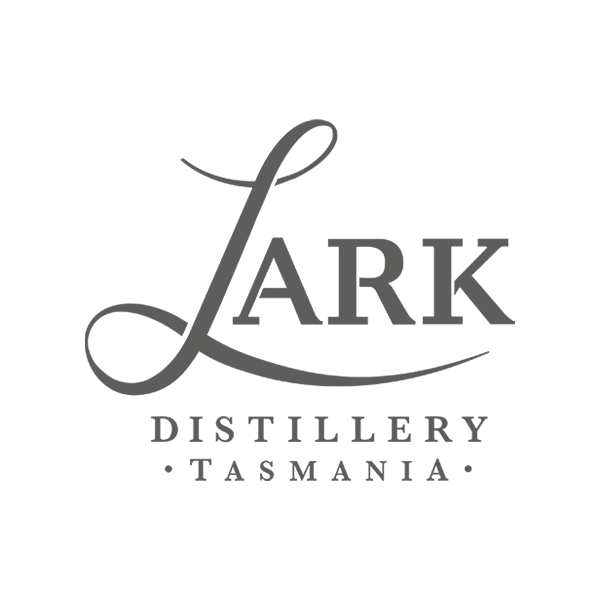
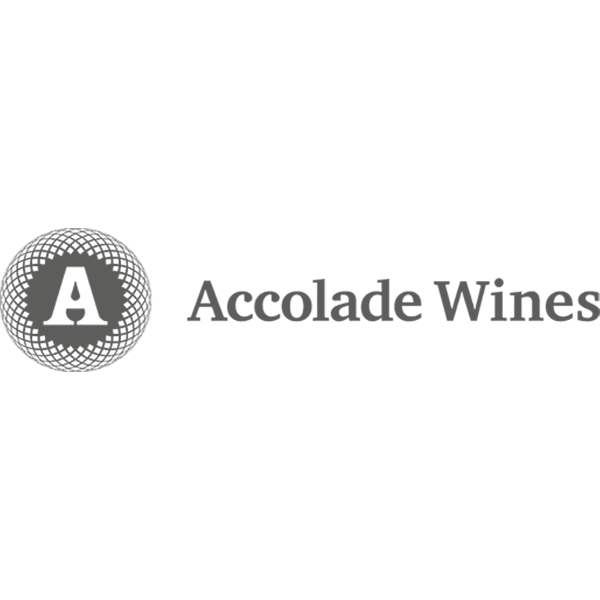
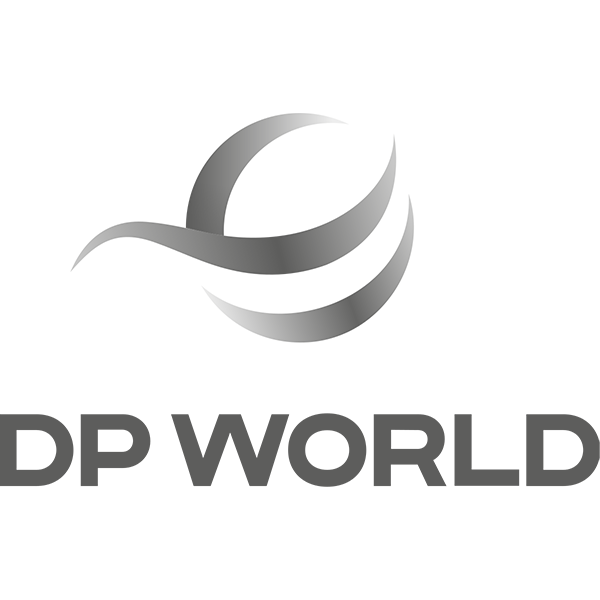
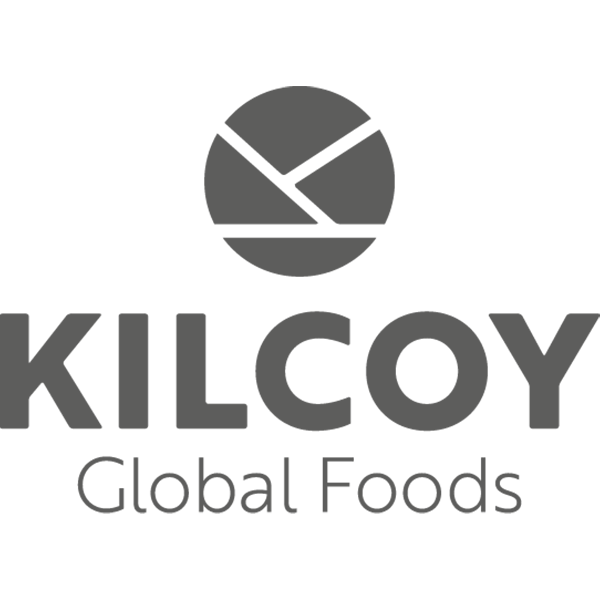
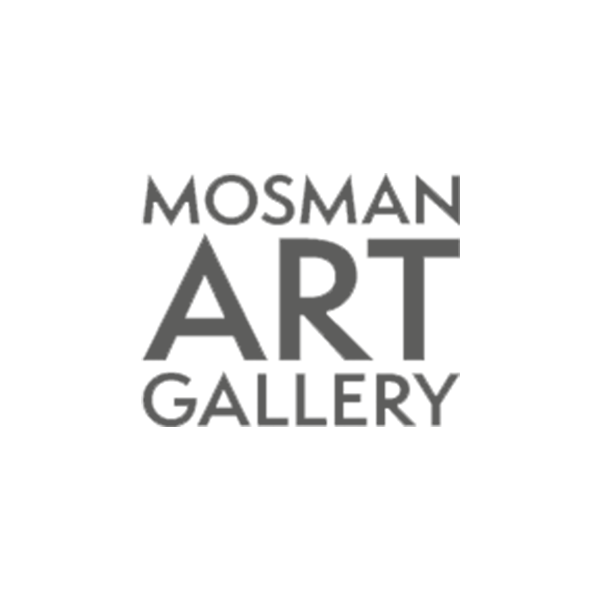
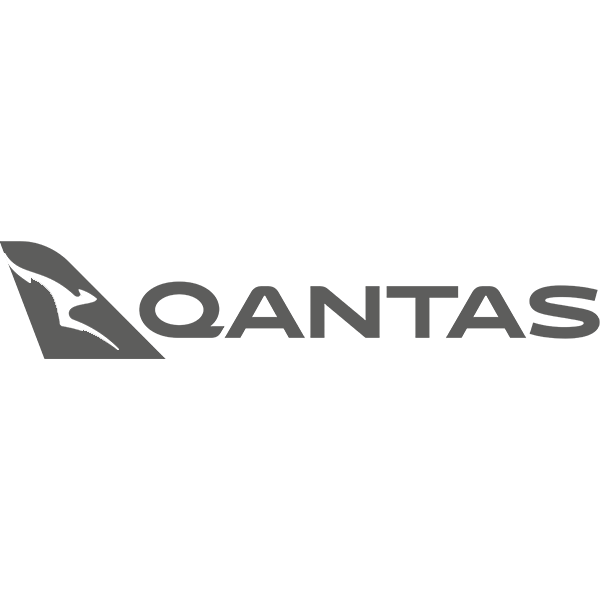
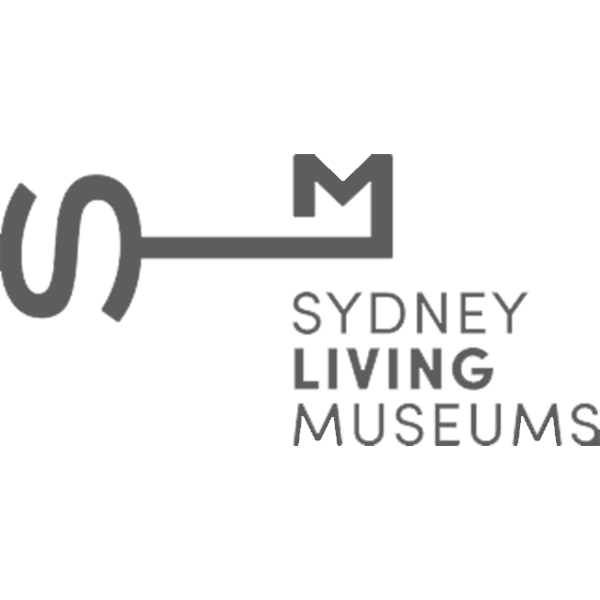
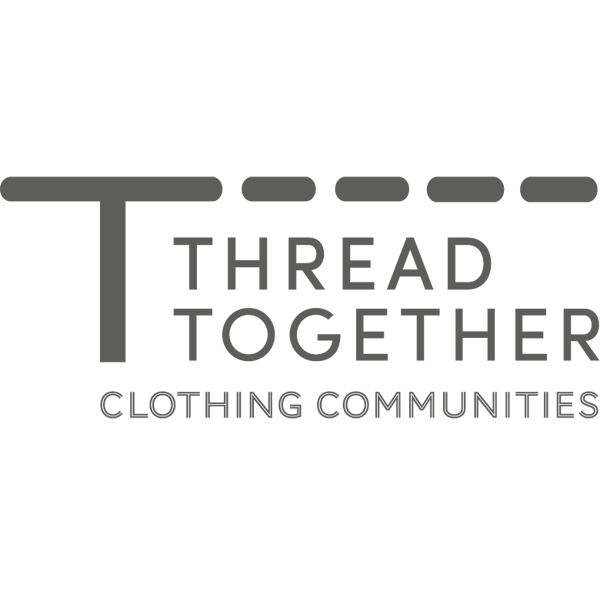